Core Technology
Core technology is developed to continuously improve the capabilities of the lab so that researchers can hit the ground running with their projects. A core technology can take an experienced professional weeks, months or years and significant resources to develop. Core technology development must be properly documented to teach valuable research and development skills, share practical mistakes and observations, and generate more return on investment. UHNF core technology is shared openly to promote our capabilities and support our community.
Core Technology Development
The cost of core technology development depends on experience, skill, knowledge and core technologies. For example, after the installation of the nanoimprint tool, some basic training from the manufacturer, a few independent experiments and some discussion with experienced researchers, it was evident that the practice of nanoimprinting is far more difficult than advertised. As it turns out, it took approximately 1 year to develop the supporting core technologies needed to develop a procedure to reliably perform nanoimprinting that can be taught to new researchers in 30 minutes.
The development of this technology has lead to the following new capabilities:
- Custom Mold Fabrication
- Anti-stick Coating
- Thermal Nanoimprinting with PMMA
- Mold and Sample Cleaning
In addition, UHNF staff has acquired expertise in thermal nanoimprinting technology. This allow us to provide more accurate research advice and more easily troubleshoot user problems.
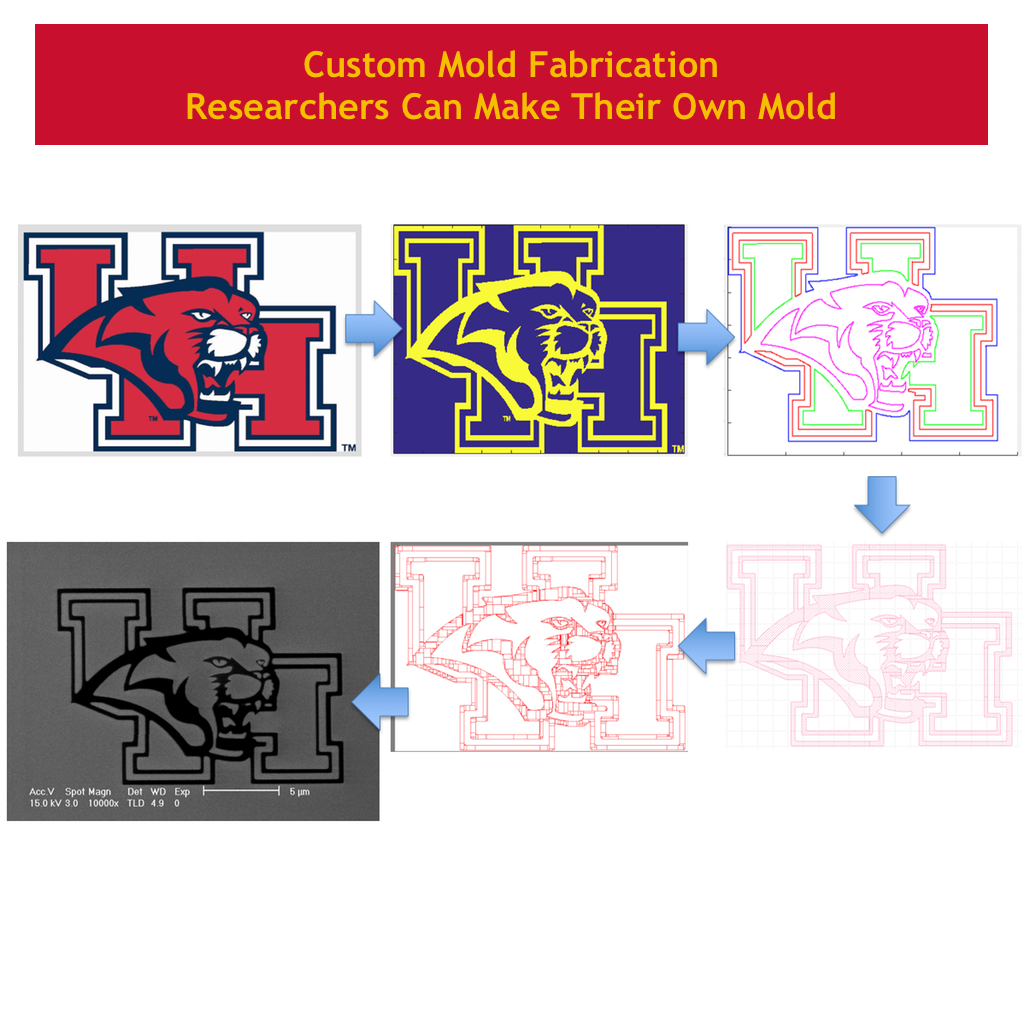
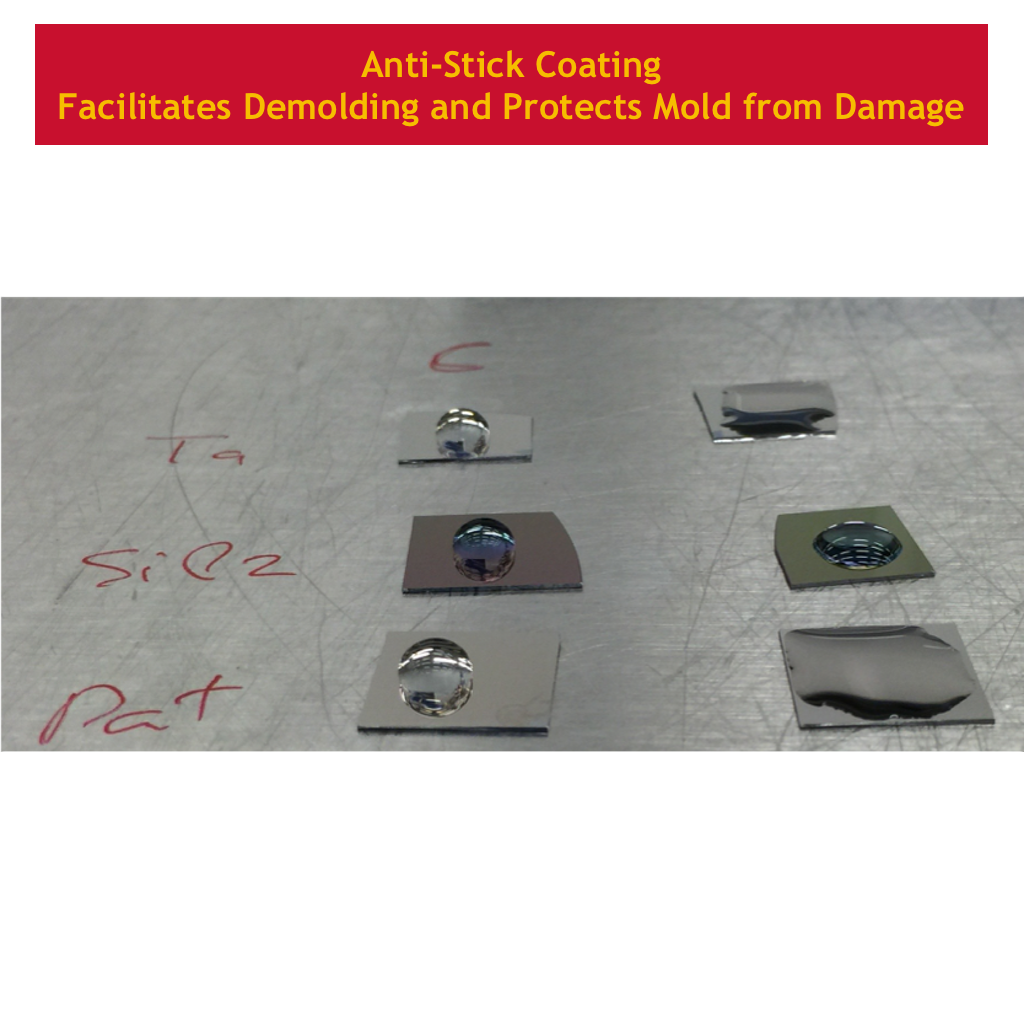
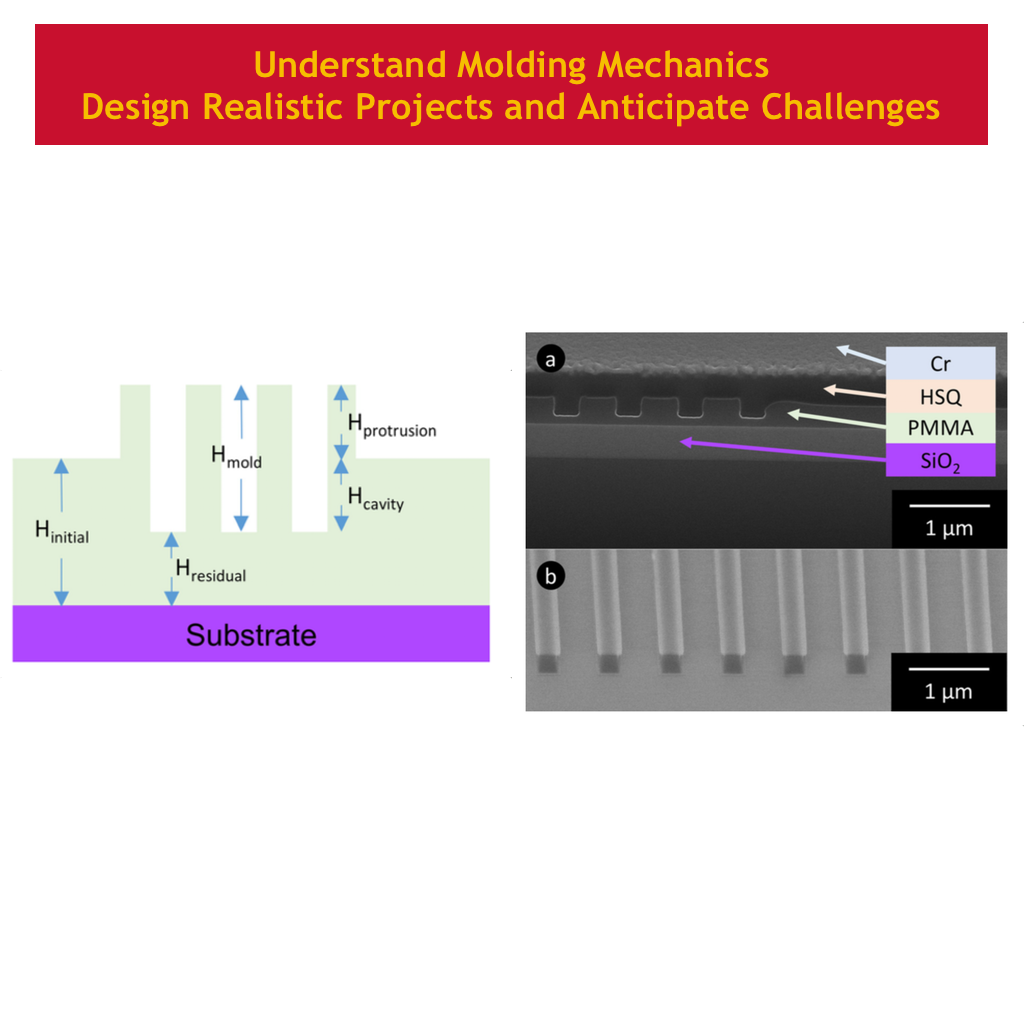
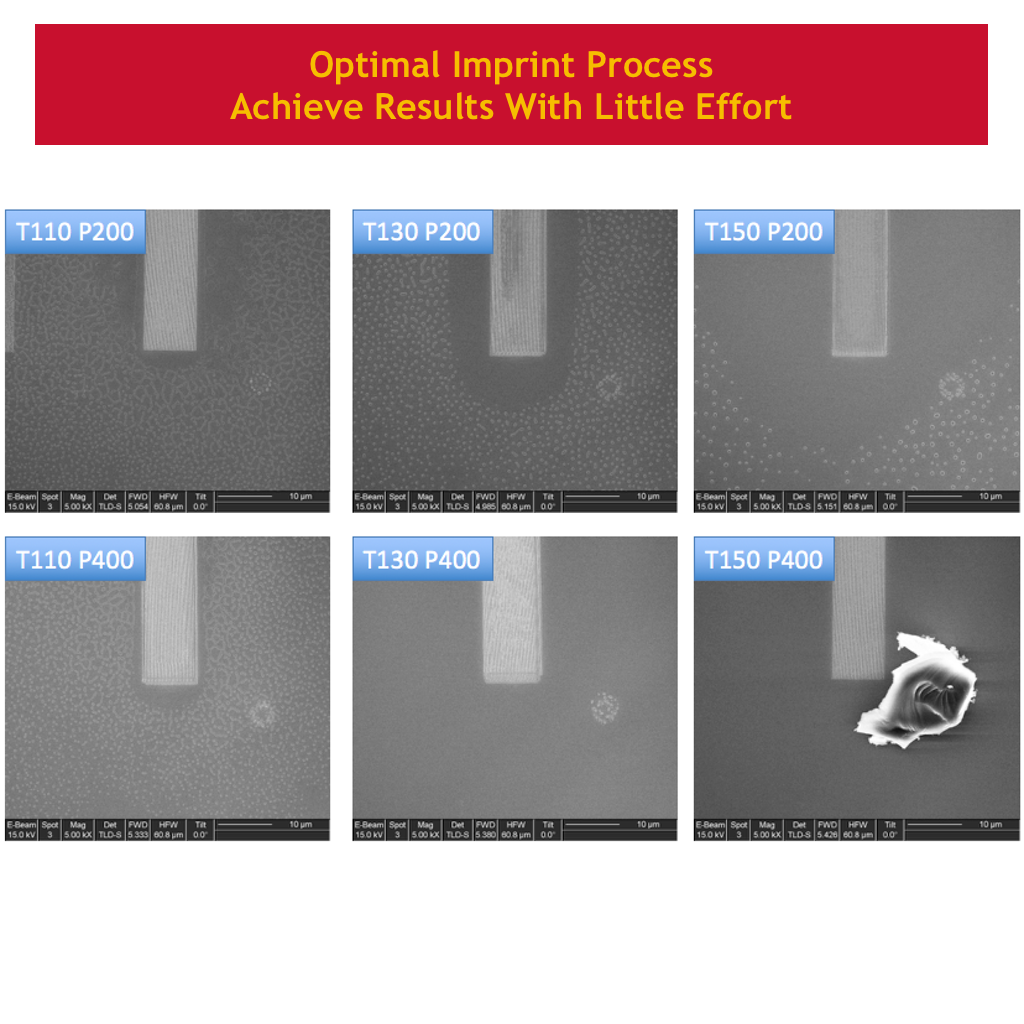
Core Technology
Name | Description | Technology |
---|---|---|
MMA/PMMA Bilayer Resist | MMA/PMMA is a bilayer electron beam resist where the MMA layer is beneath the PMMA layer. After exposure and development, MMA patterns are approximately 120 [nm] wider than PMMA patterns. This feature is great for producing clean structures via lift-off. | Electron Beam Lithography |
PMMA/HSQ Bilayer Resist | PMMA/HSQ is a bilayer electron beam resist where the PMMA layer is beneath the HSQ layer. Electron beam lithography is used to pattern the HSQ layer. Then a reactive ion etcher is used to etch through the PMMA layer while the HSQ layer is unaffected. This process provides excellent control over the amount of undercut in PMMA. | Reactive Ion Etching |
SiO2/HSQ Etch | HSQ is a material that can easily be patterned that shares similar qualities to SiO2. From this experiment, we discover that the ICP Power can be selected to achieve an etch selectivity between SiO2 and HSQ of 1 to 1 or 0.6 to 1. | Reactive Ion Etching |