Equipment Controls and Automation
Equipment controls and automation provides increased productivity, reduces maintenance time and costs, and enhanced capabilities. Besides providing these basic features, our design philosophy is to develop a product that is easy to use, easy to maintain and easy to update. This design philosophy is derived from over a decade of experience developing controls and automation for over 6 different scientific equipment.
How It Works
1. Contact Us
Contact us to discuss your needs for equipment automation
2. Proposal
We will communicate with all stakeholders to determine their needs and wants to draft a specification and estimate the cost
3. Remote Development of a Mock System
We will develop a mock system remotely without accessing the equipment. Stake holders may play with the mock system and provide feedback
4. Installation and Commissioning
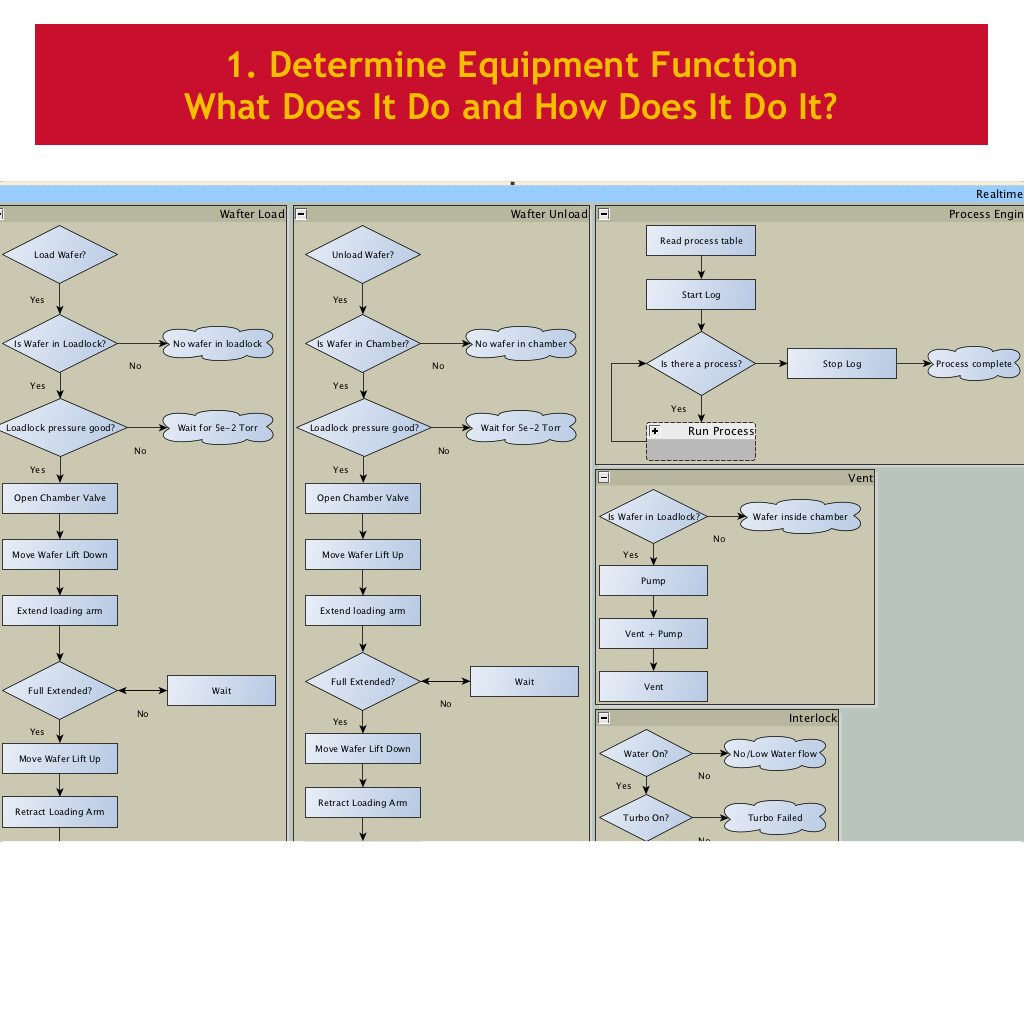
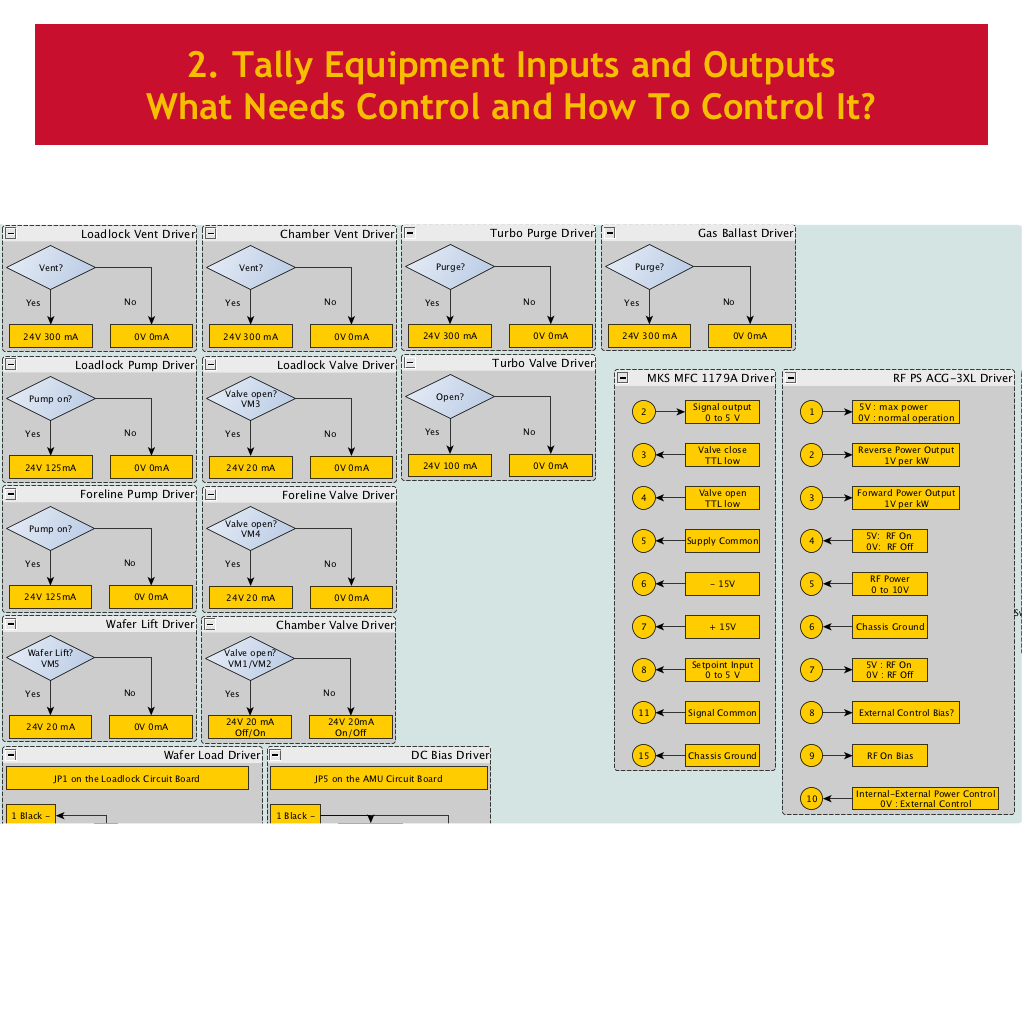
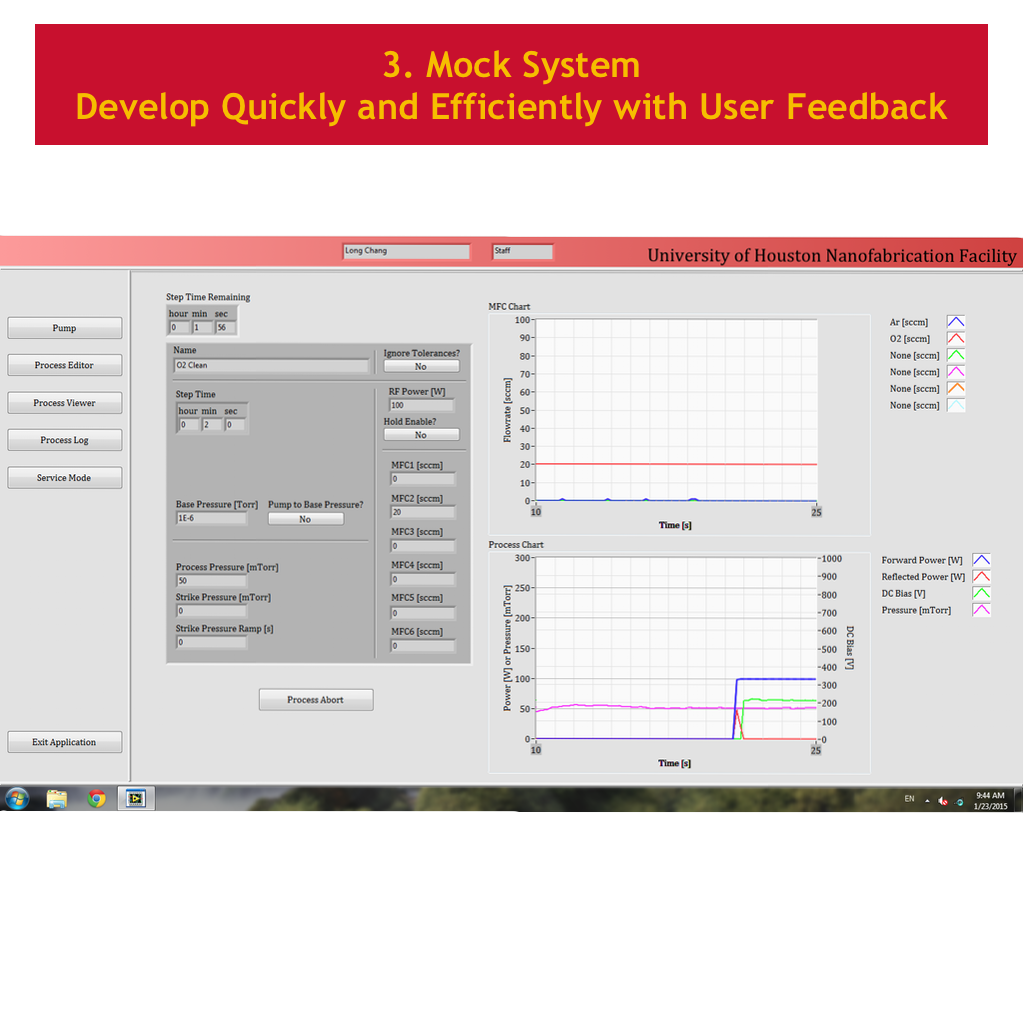
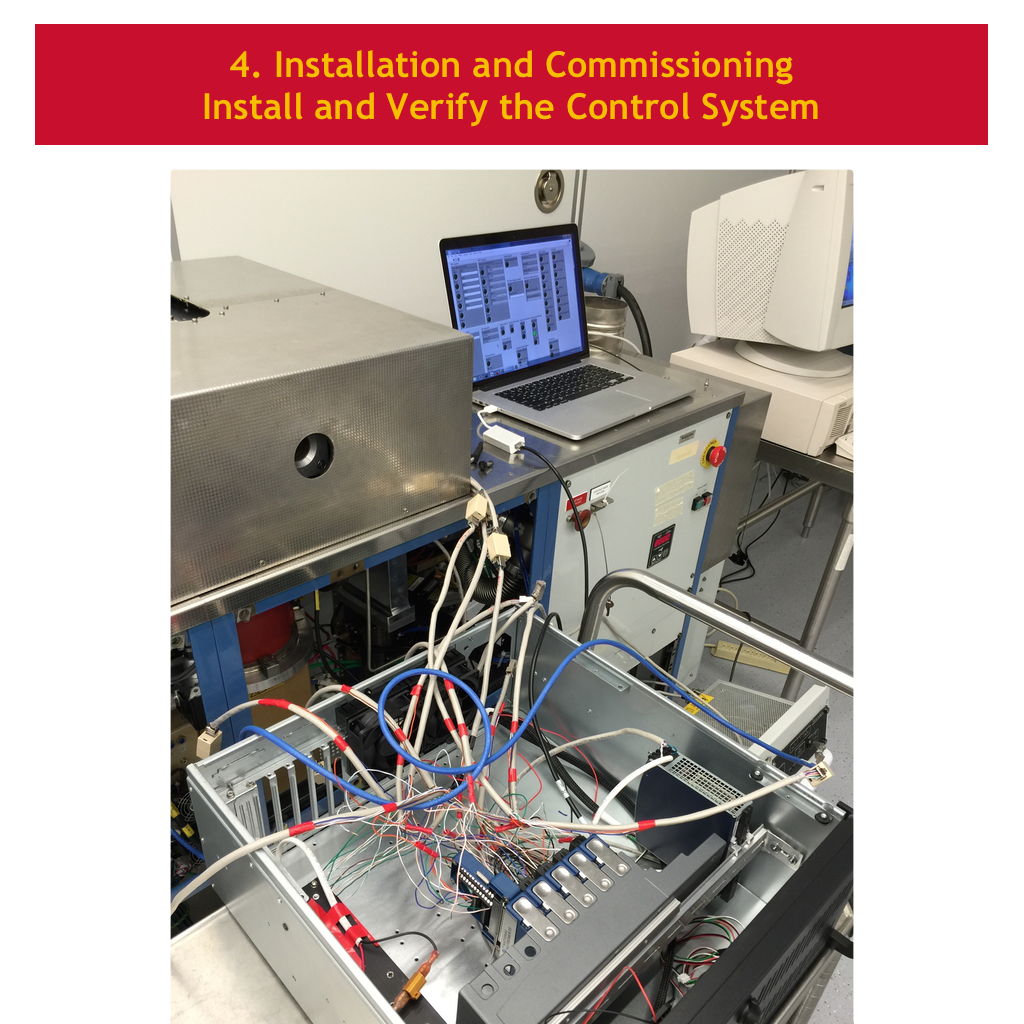
Examples
GMR Testing Module for an AFM
An atomic force microscope provides a platform for researchers to interact with microscopic samples. We imagine an experiment to use the AFM probe to suspend a magnetic nanoparticle above a GMR sensor to characterize its response. The Asylum Research AFM software runs on Igor which is conveniently a programming platform. Instead of taking the comfortable approach using what we know, we learned how to program on the Igor platform to seamlessly integrate our program with the AFM software. This enables any of our AFM operators to access the module with little additional training. In addition, it is trivial to implement IV curves measurements to the AFM system in the future.
The Asylum Research AFM software is open source which provides researchers who can use the Igor platform tremendous control over the equipment. As a custodian of many scientific equipment, it is often the software that limits what users can do.
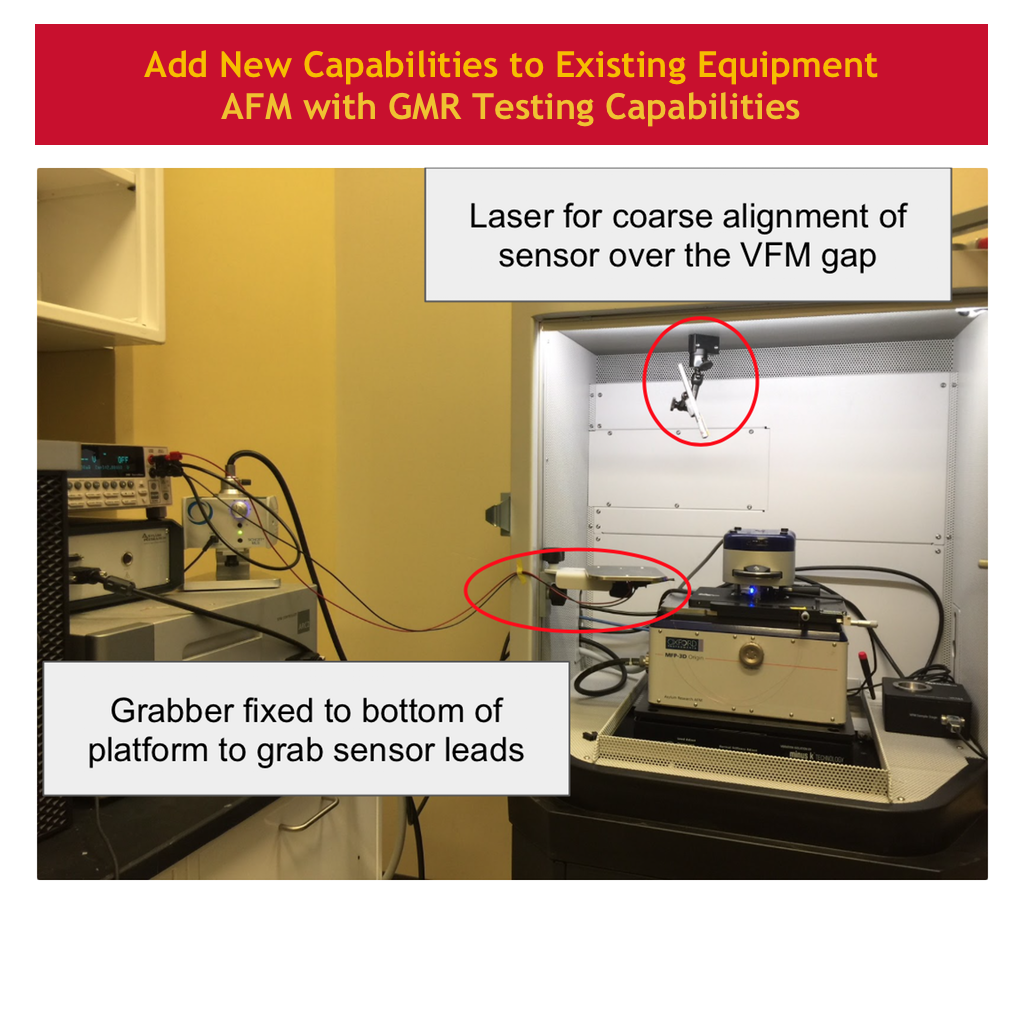
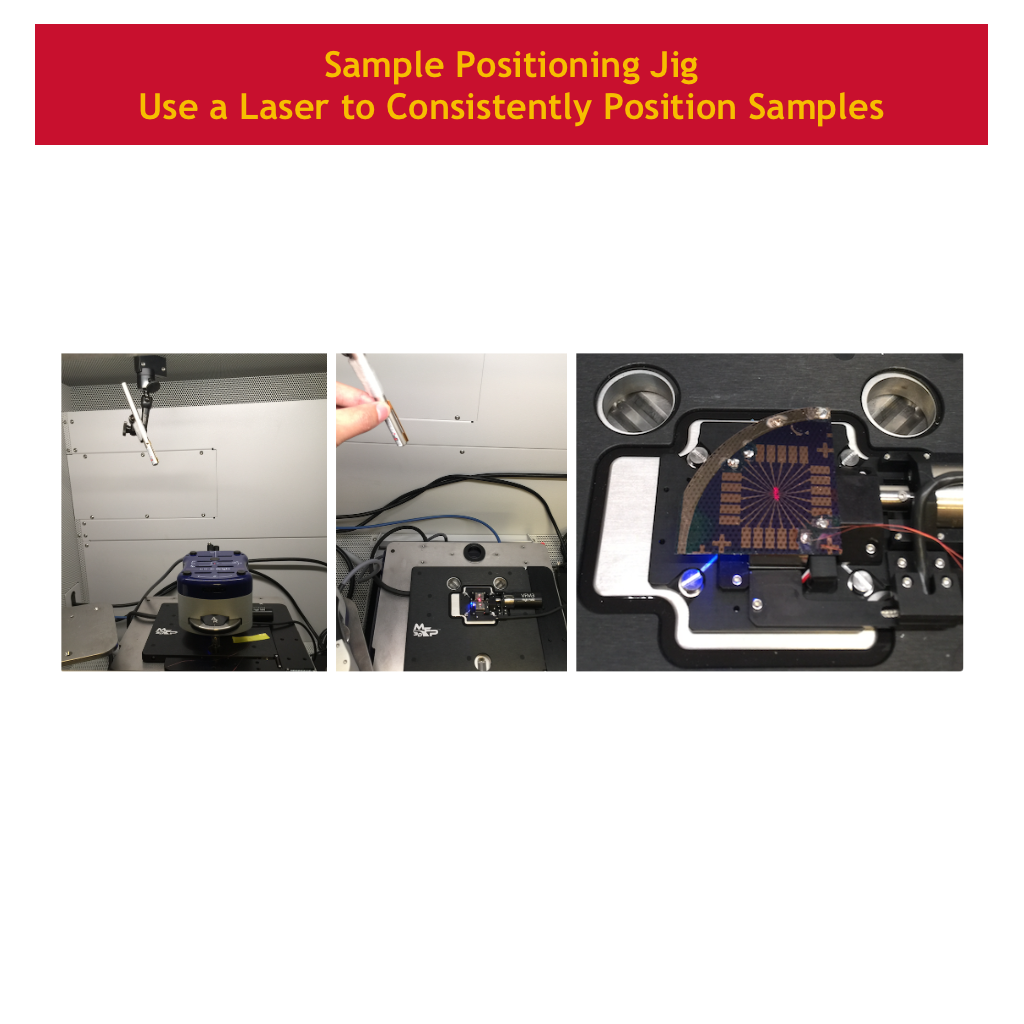
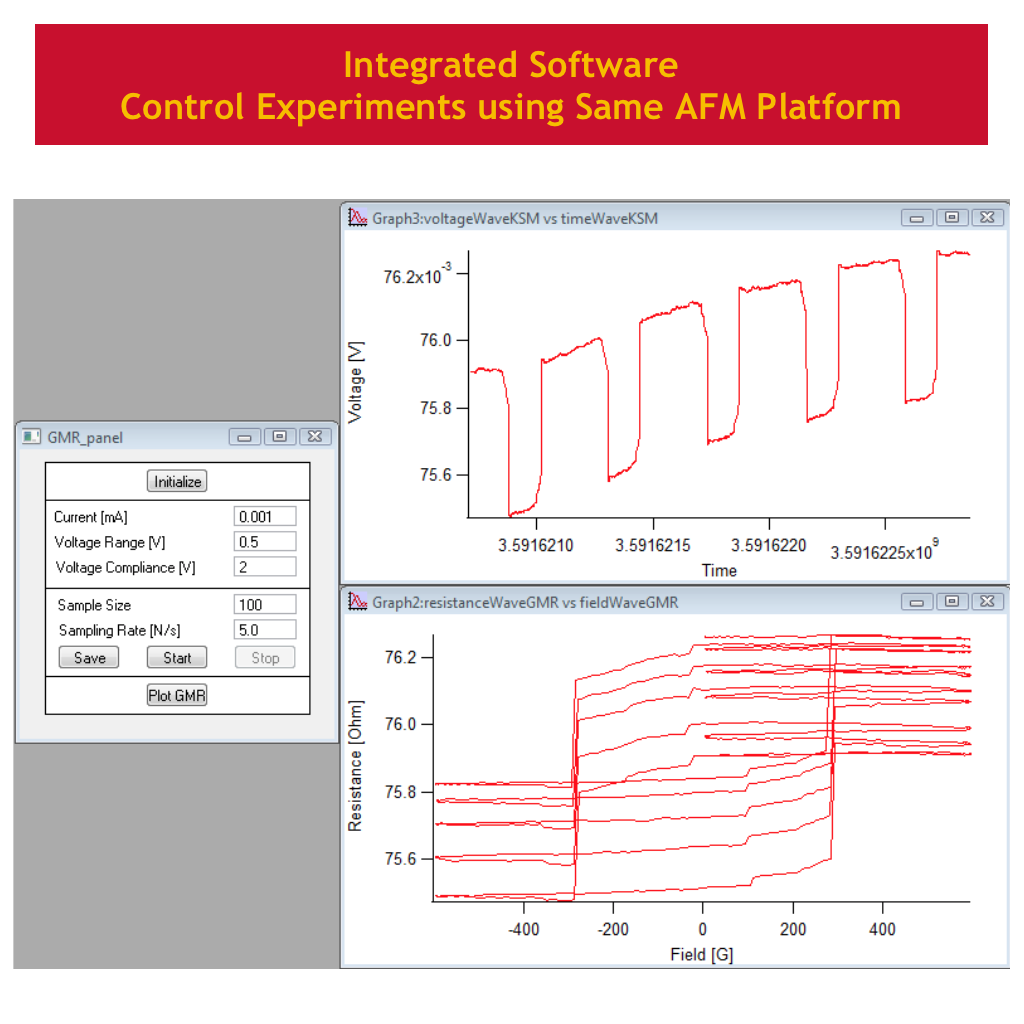
Reactive Ion Etcher
In 2013, our Oxford Instrument Plasmalab 100 reactive ion etcher had a recurring problem with the pressure control and only 75% of the user interface was accessible. The manufacturer could replace the obsolete control system, but could not fix the interface issue on the obsolete computer. Instead of partially fixing the problem with obsolete components, we decided to try to build our own control and automation system (CAS) using modern technology.
The CAS was developed using LabVIEW’s Compact RIO programmable automation control. We are familiar with LabVIEW programming and we were able to quickly and successfully develop a very simple mock system using the LabVIEW RIO Eval Kit. Developing the real system took approximately 4 months from the initial assessment and reverse engineering of the controls for 20 components to the third overhaul of the labVIEW program. The entire application was developed with negligible interruption of the equipment. Since its installation and commissioning, the system was patched once to add a new capability. The patch took less than half a day to develop and install which is a testament to the ease of updating the program.
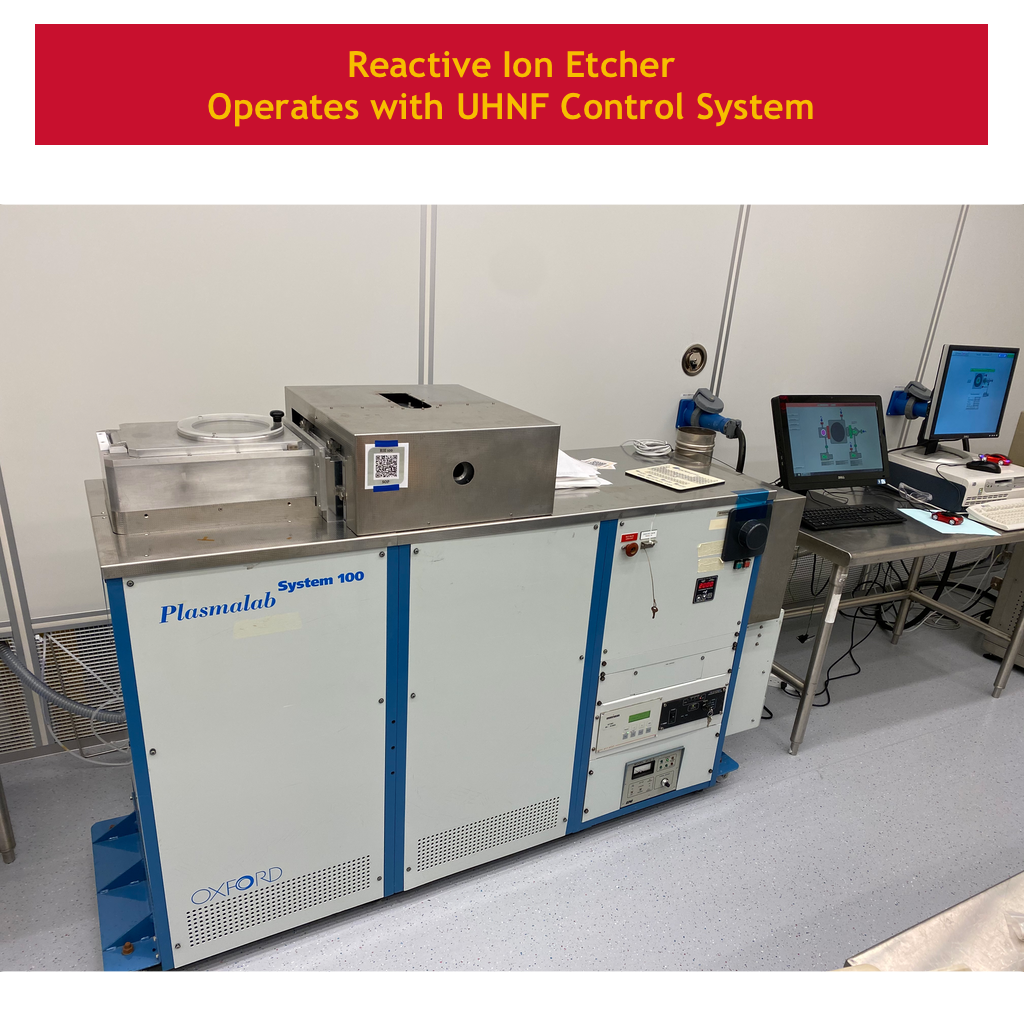
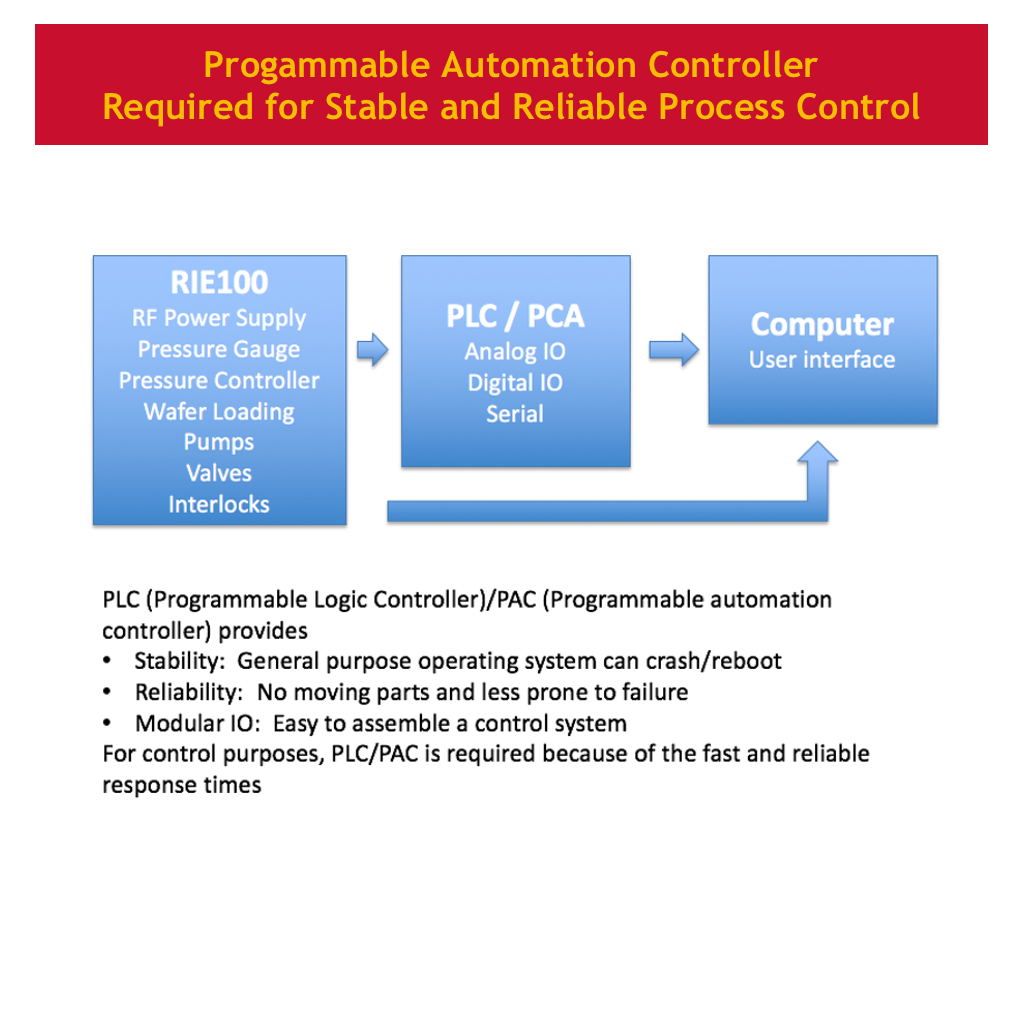
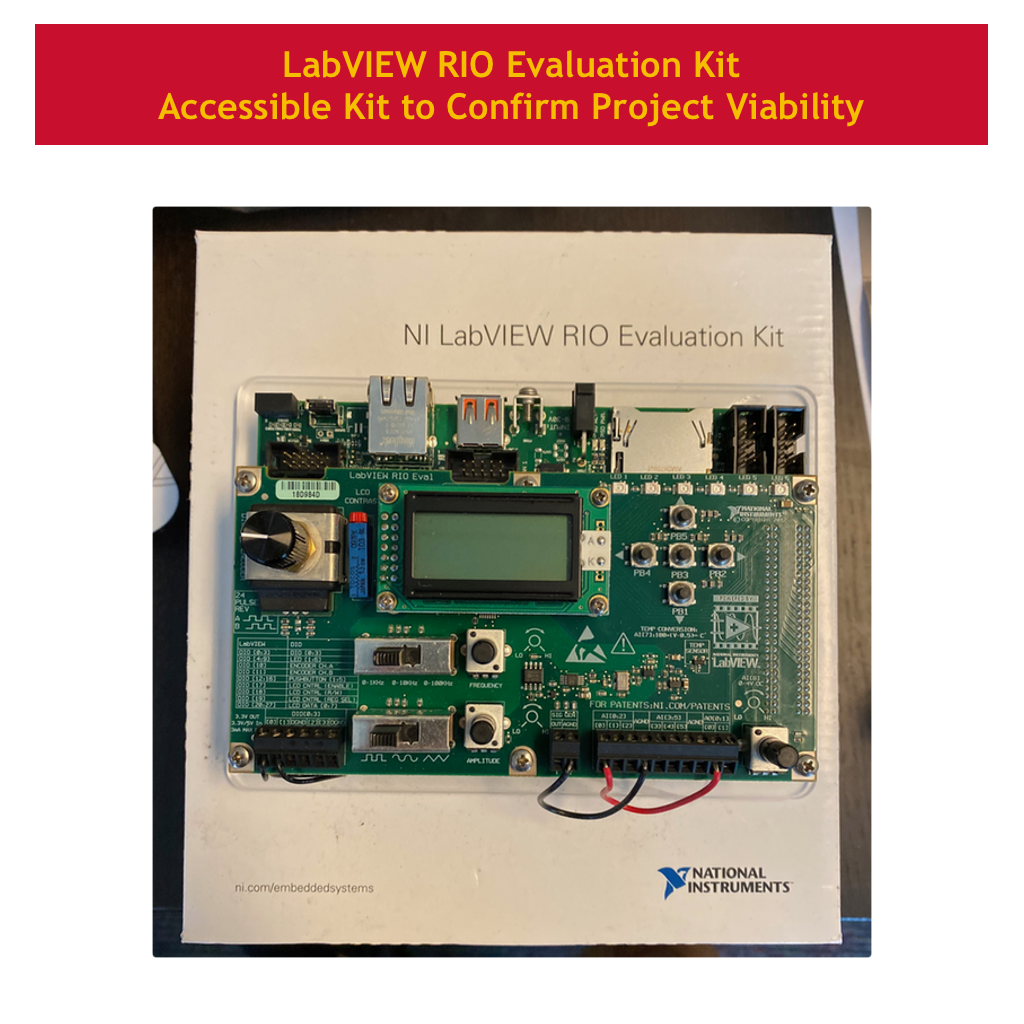
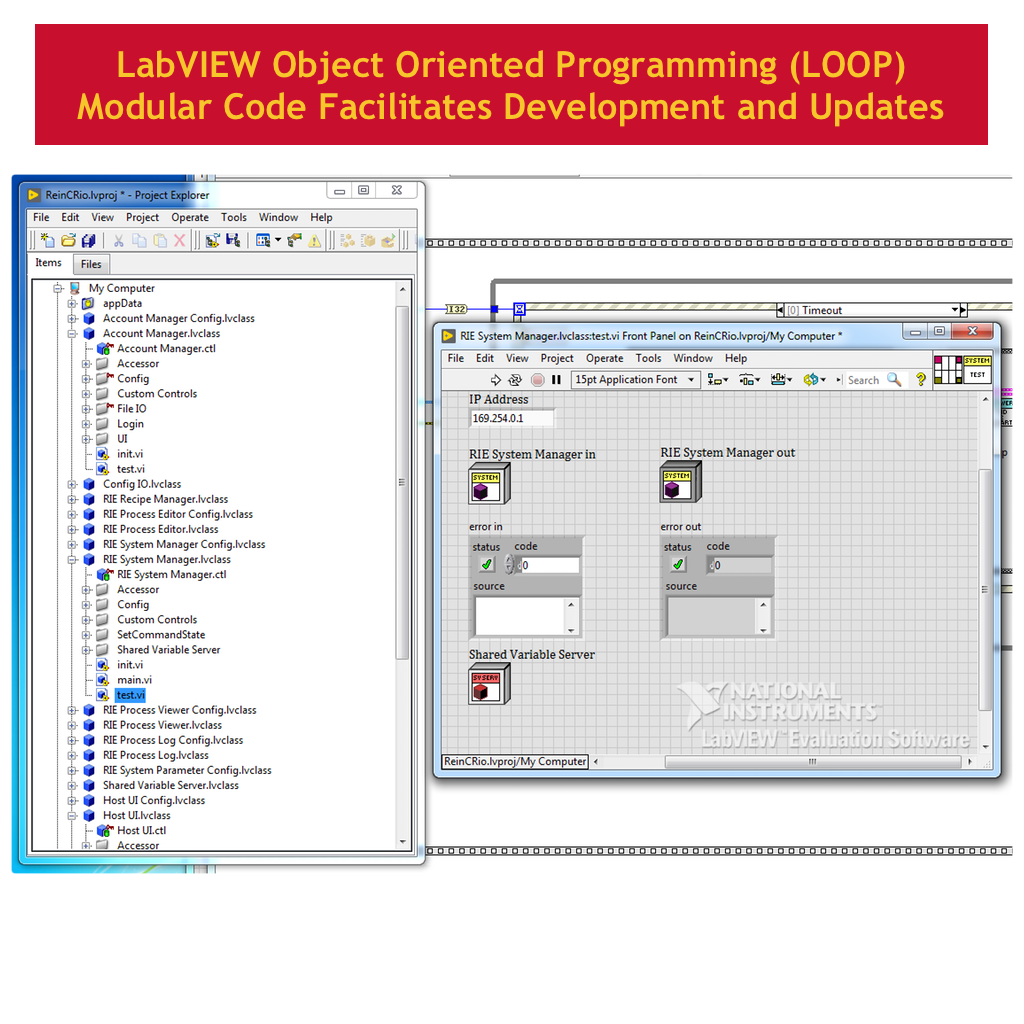
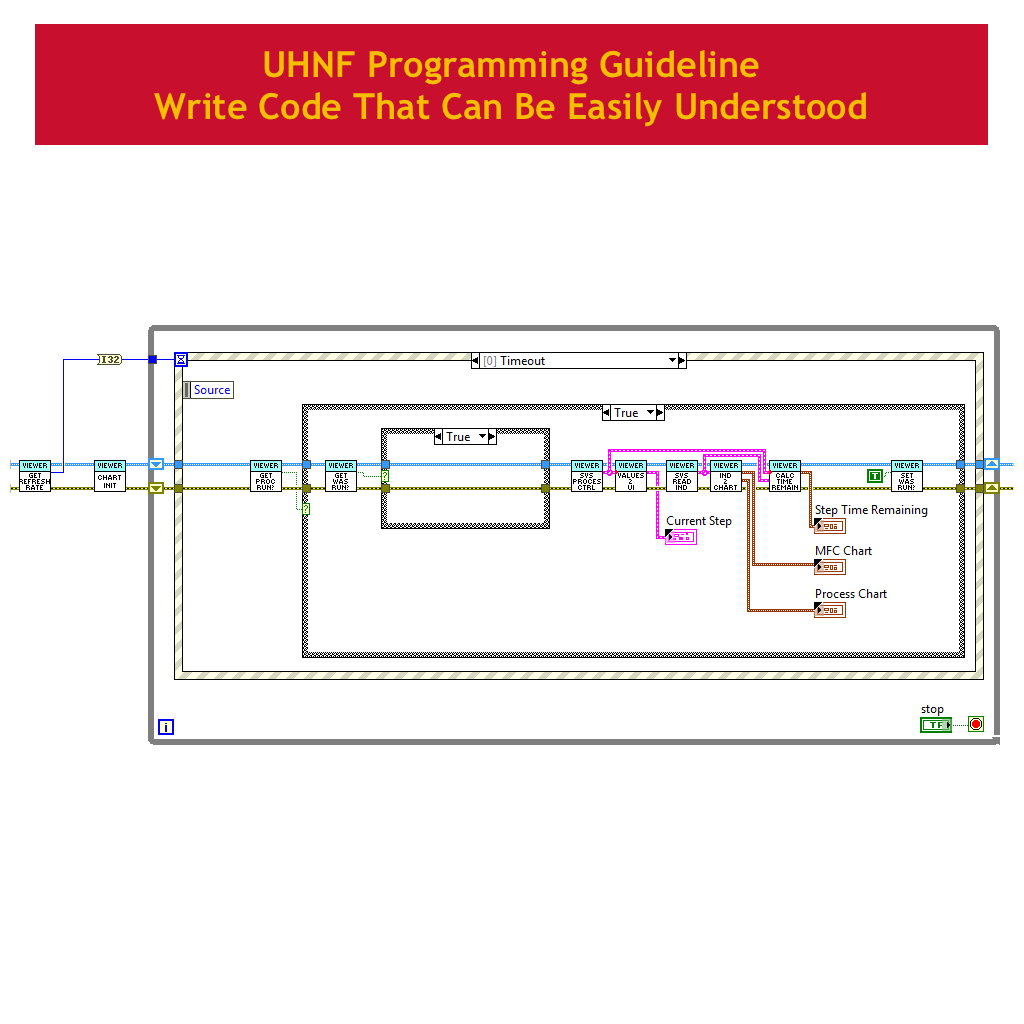
Scanning Magnetoresistance Microscope (SMRM)
A scanning magnetoresistance microscope was designed and developed to characterize the switching properties of bit patterned media, a contending successor to perpendicular hard disk media at the time. The SMRM is similar to a scanning probe system like an atomic force microscope (AFM), but uses a perpendicular recording head instead of a probe. The recording head contains a GMR sensor that transduce a magnetic field to a voltage, enabling the SMRM to capture a magnetic image of the sample. The recording head also contains a microscopic electromagnet that can generate up to 24 kOe of magnetic field. The ability of the SMRM to read and write a magnetic material makes it an ideal system for probing the switching properties of bit patterned media which contain magnetic bits that are 100 nm in diameter or smaller.
This project demanded speed, precision and stability. This was achieved by addressing each problem through measurement and optimization. The performance of each component is pushed to the limit to deliver a user friendly system that produces reliable data in a few minutes.
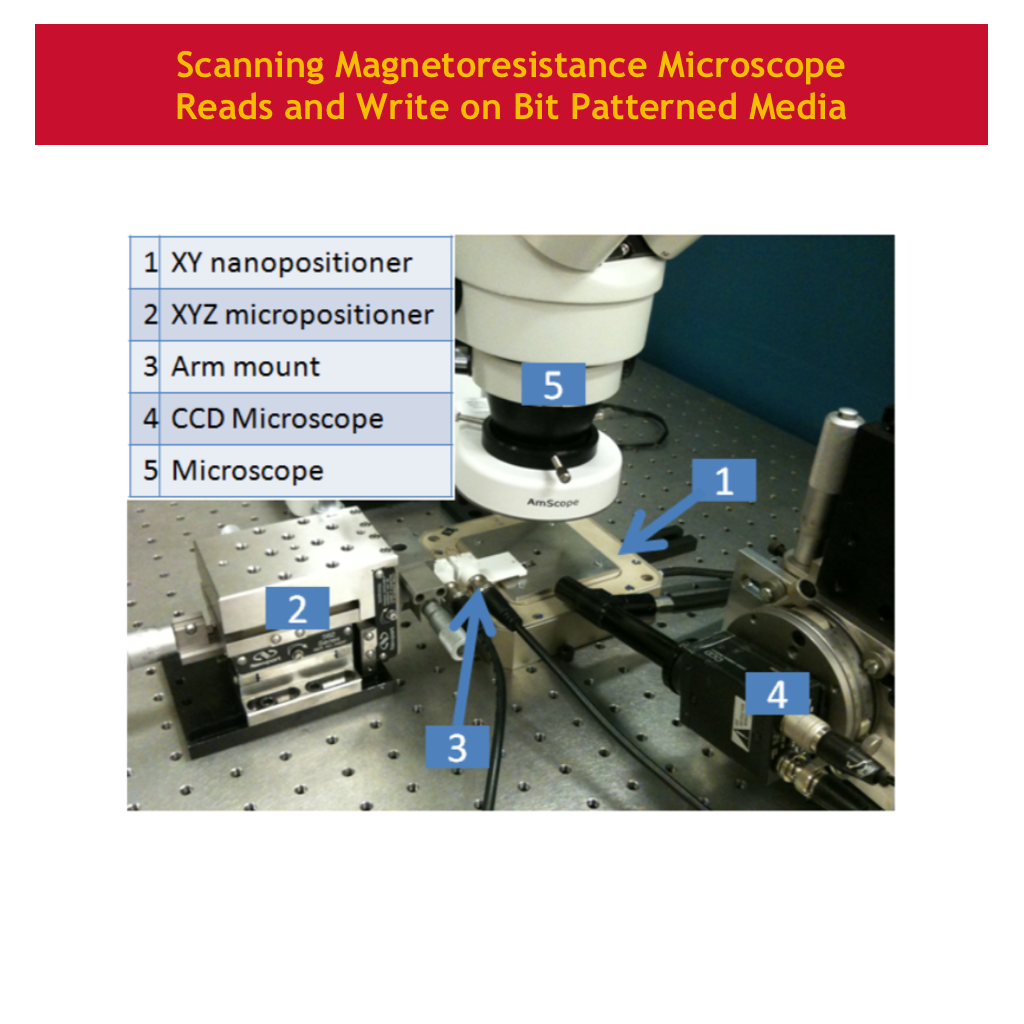
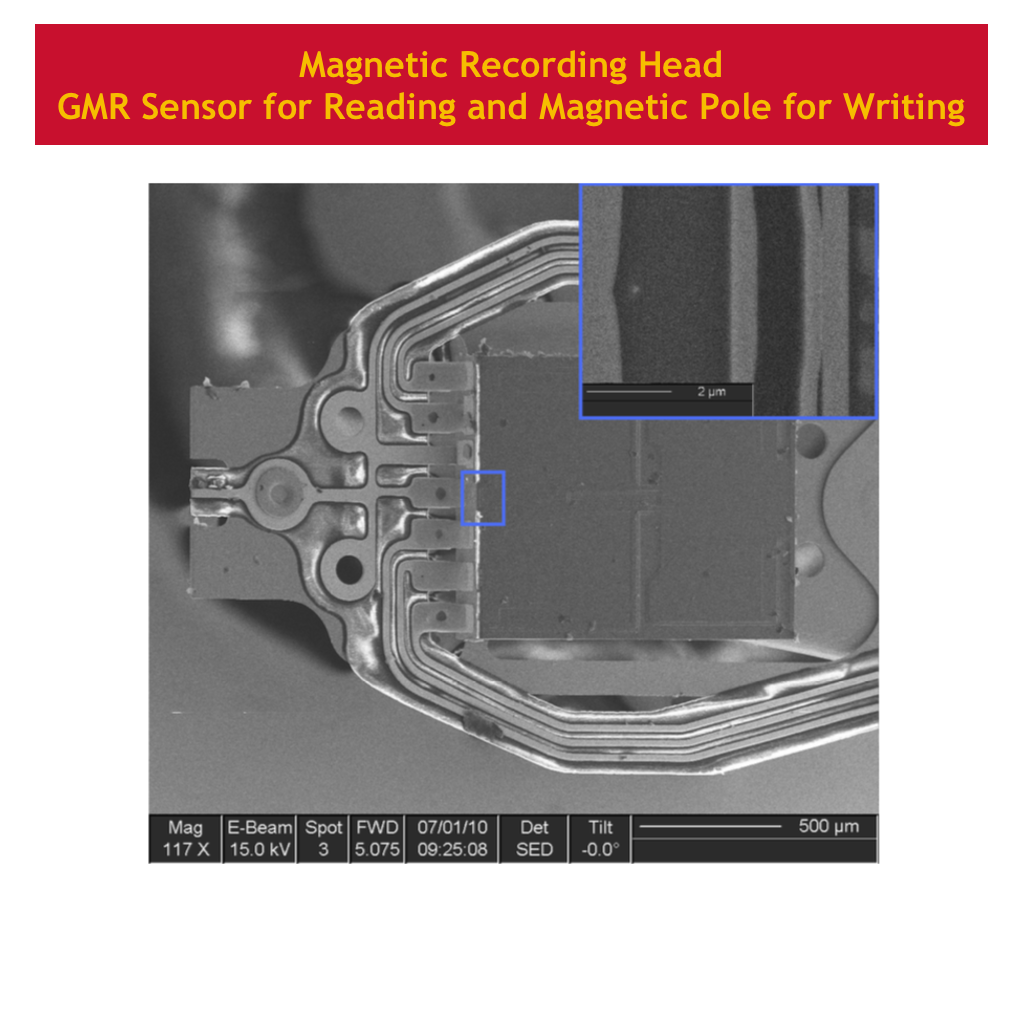

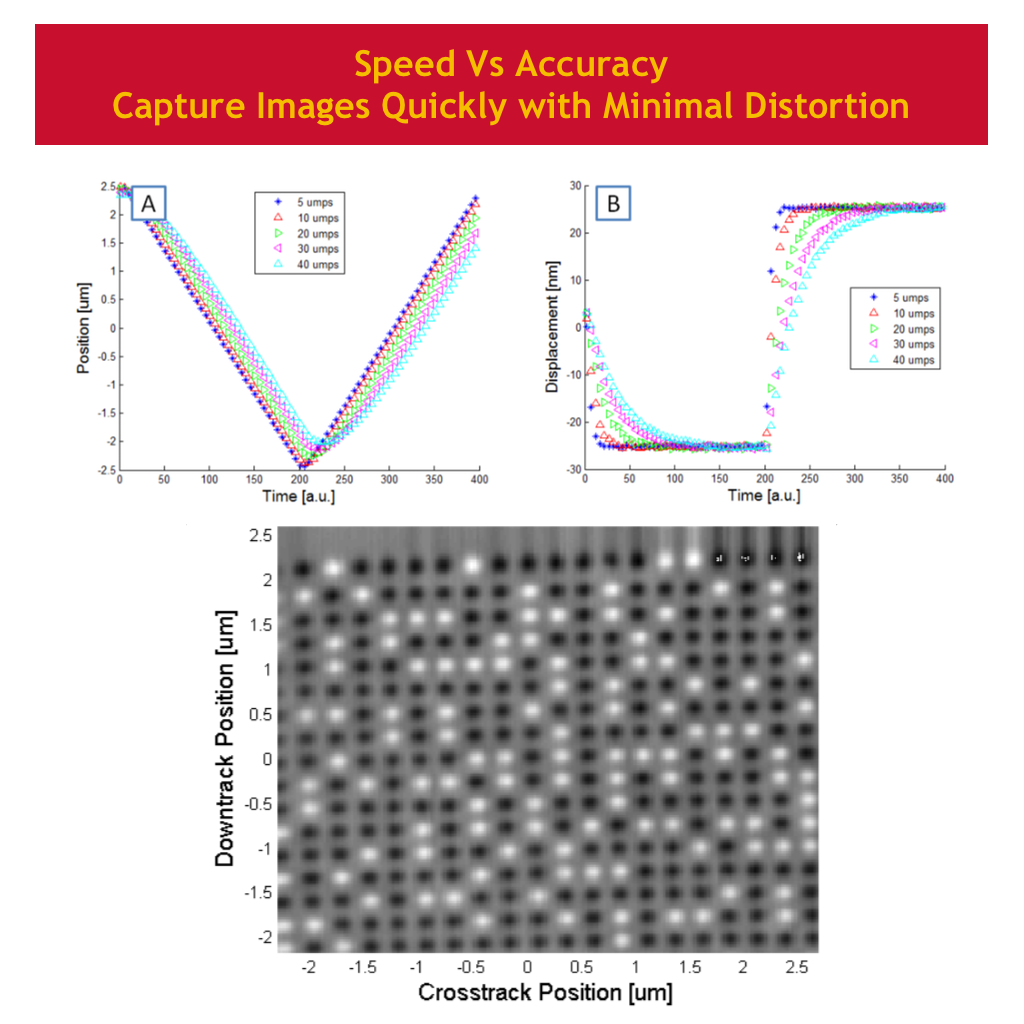
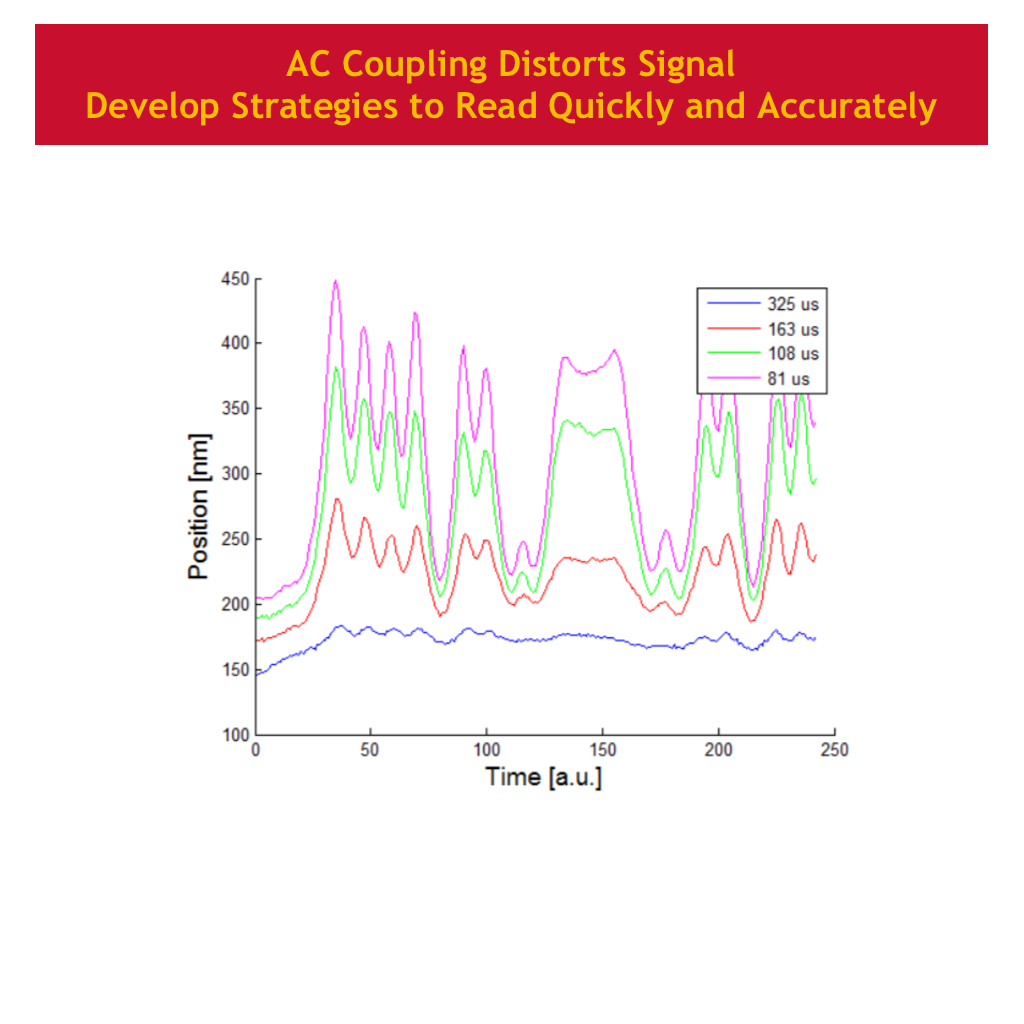
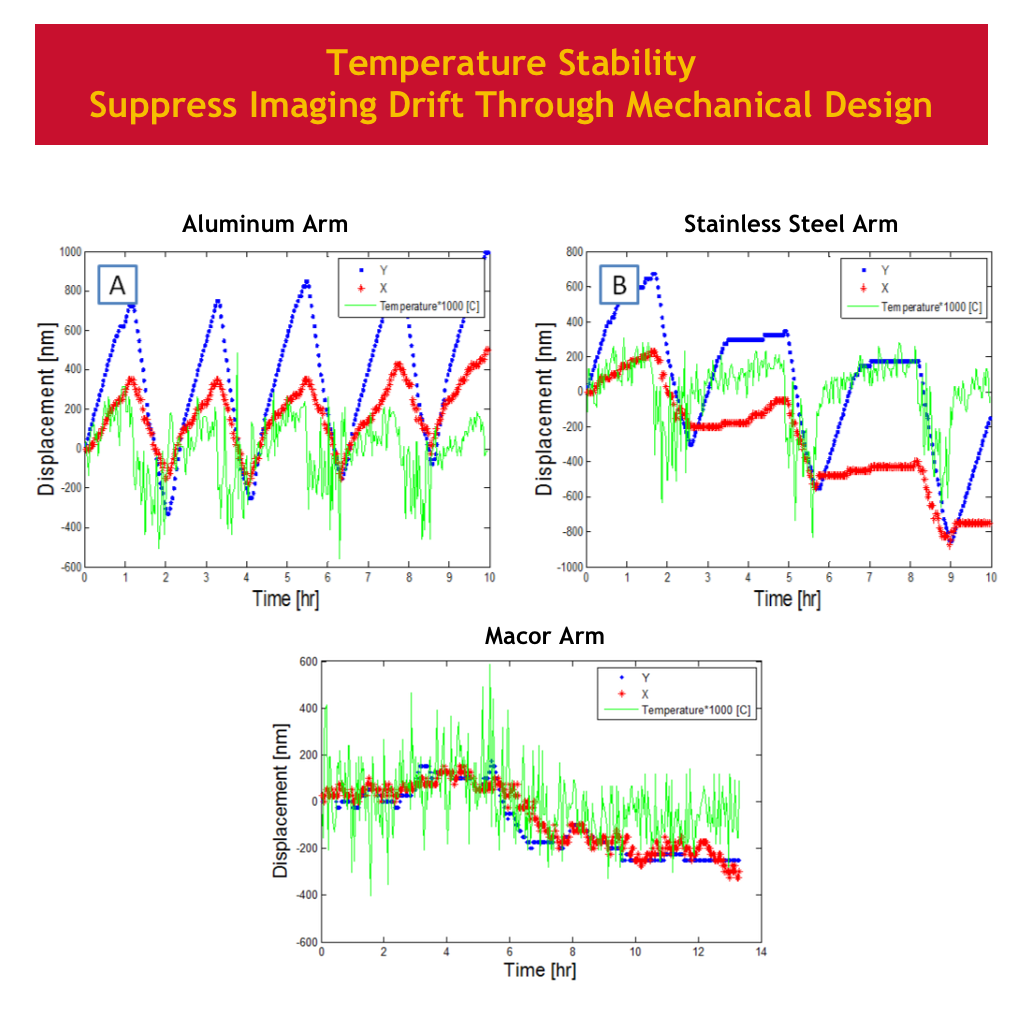
Polar Magneto-Optical Kerr Effect (PMOKE)
Prototype bit patterned media can not be characterized with conventional equipment. The amount of magnetic material in a sample of bit patterned media (BPM) is too little for magnetometers. BPM is fabricated using a direct write electron beam lithography technology with low throughput, limiting the sample area to 170 x 170 μm2. In a PMOKE, polarized light reflecting off a smooth film undergoes a change in polarization angle proportional to the magnetic moment of the film. The design of the PMOKE focuses on minimizing the beam diameter from 1 mm diameter to below 200 μm and maximizing the signal to noise ratio.
This PMOKE system is capable of measuring a sample in under 20 seconds. It can also perform batch measurements by selecting a number of measurement points after scanning the sample. These features allowed us to fabricate and characterize multiple BPM designs on a single chip!
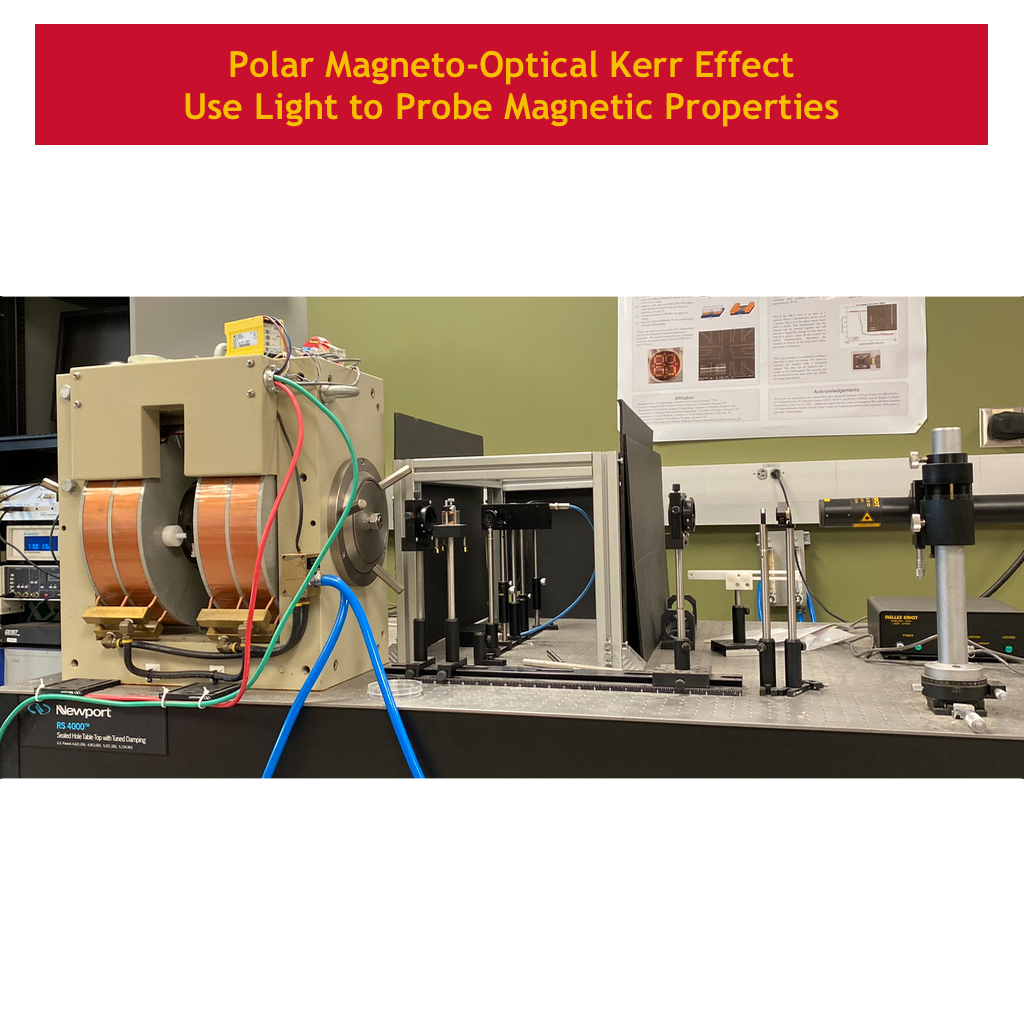
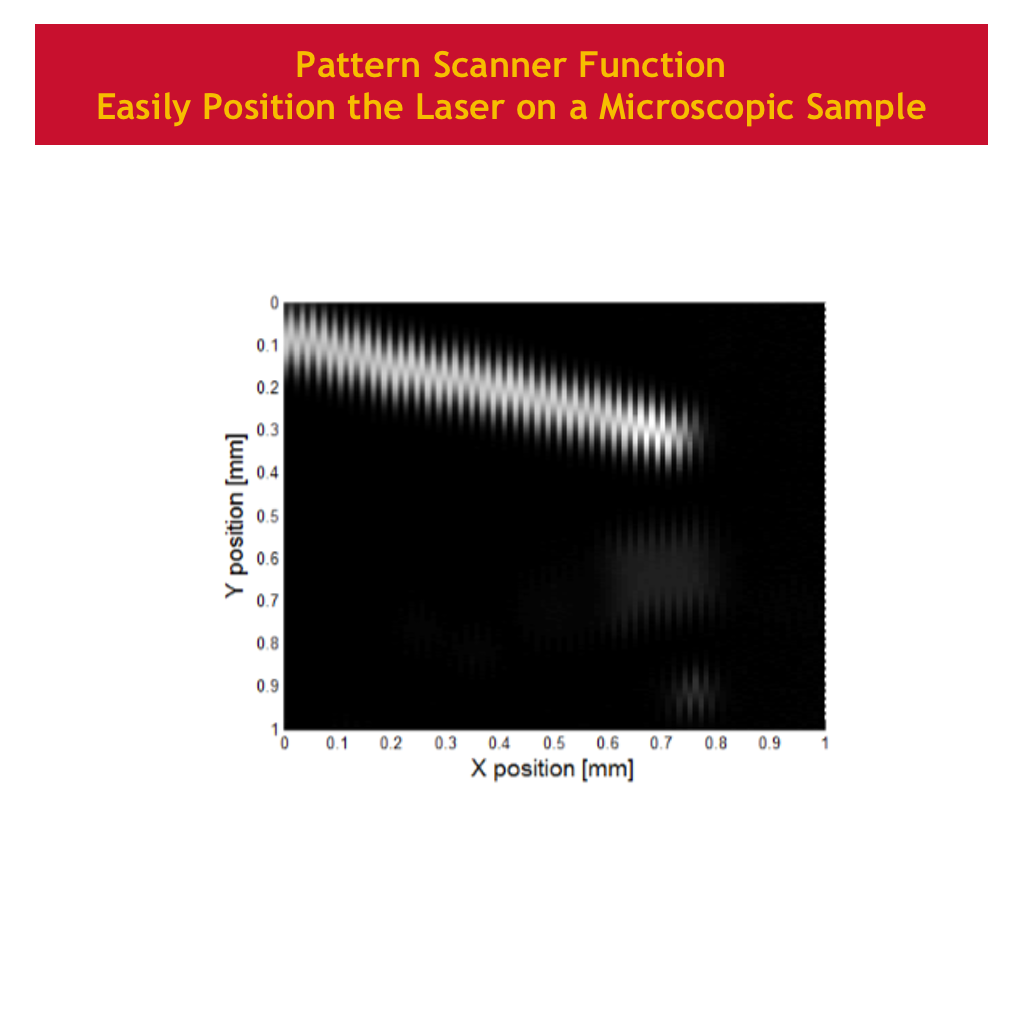
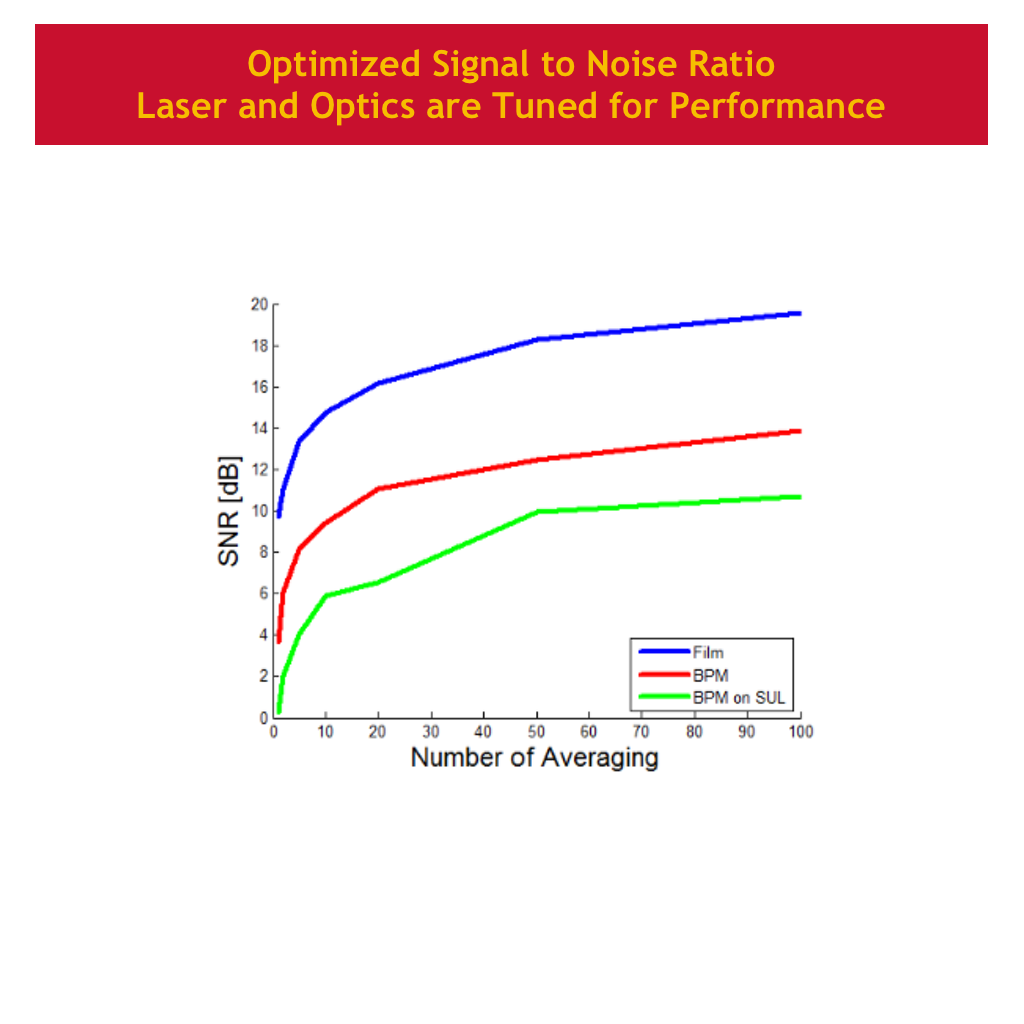