Microfabrication Service
Fabricating a device can take a professional weeks, months or years depending on their expertise, toolset capability and available core technology. As UHNF continue to expand our core technology portfolio, we are able to provide an increasing number of fabrication services.
UHNF staff are professional scientists and engineers with over a decade of experience fabricating microscopic gadgets, maintaining and hacking sophisticated scientific equipment, and developing robust core technologies. Hire us to greatly accelerate your projects.
How It Works
1. Project Specification
Contact us to inquire about your project. We will discuss the feasibility of your project and explain the risks involved. Then we will determine the specifications for the project and provide a rough estimate for the cost and lead time.
2. Quote
We will provide an itemized quote detailing the cost of the project. We charge for supplies, labor and equipment time.
3. Work Report
The work is meticulously documented to ensure quality. The report may contain inspection data, special processing information, interesting observations, recommendations for improvement, and anything the customer requests.
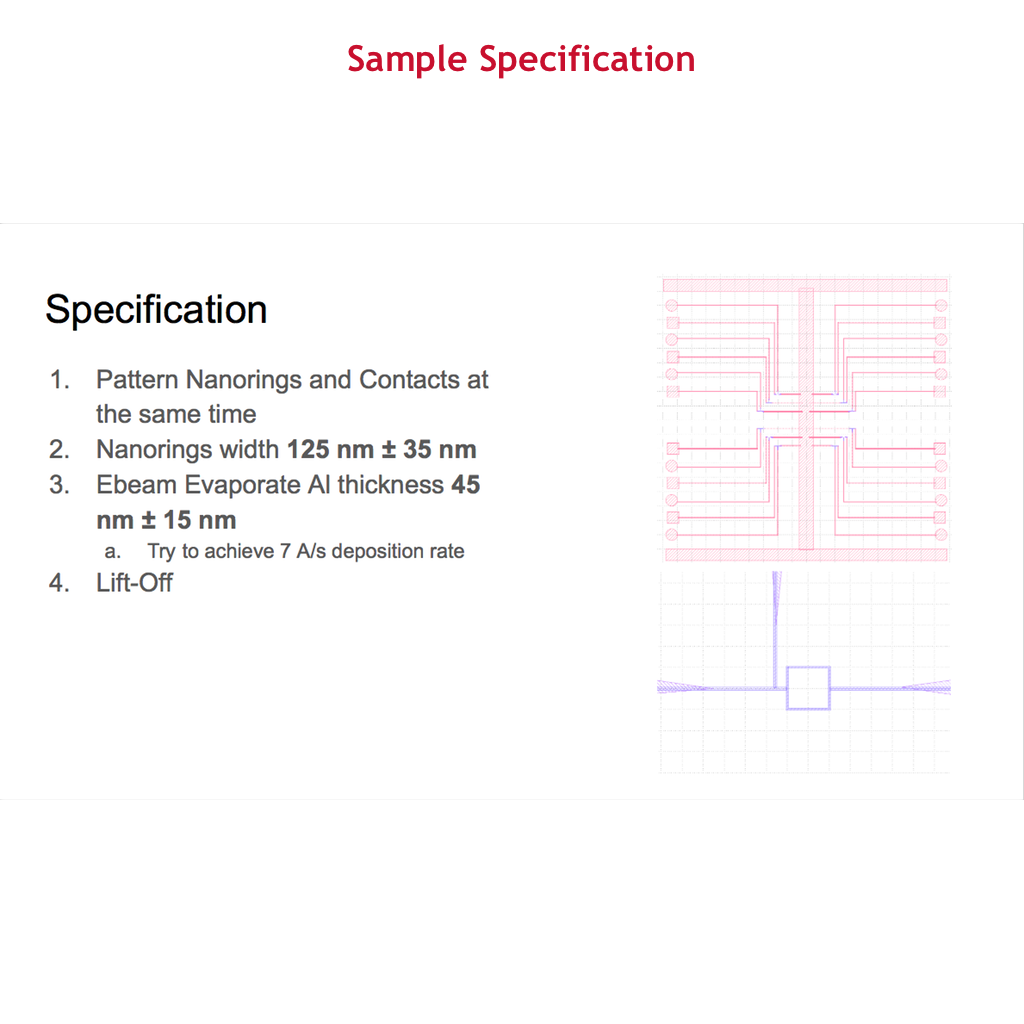
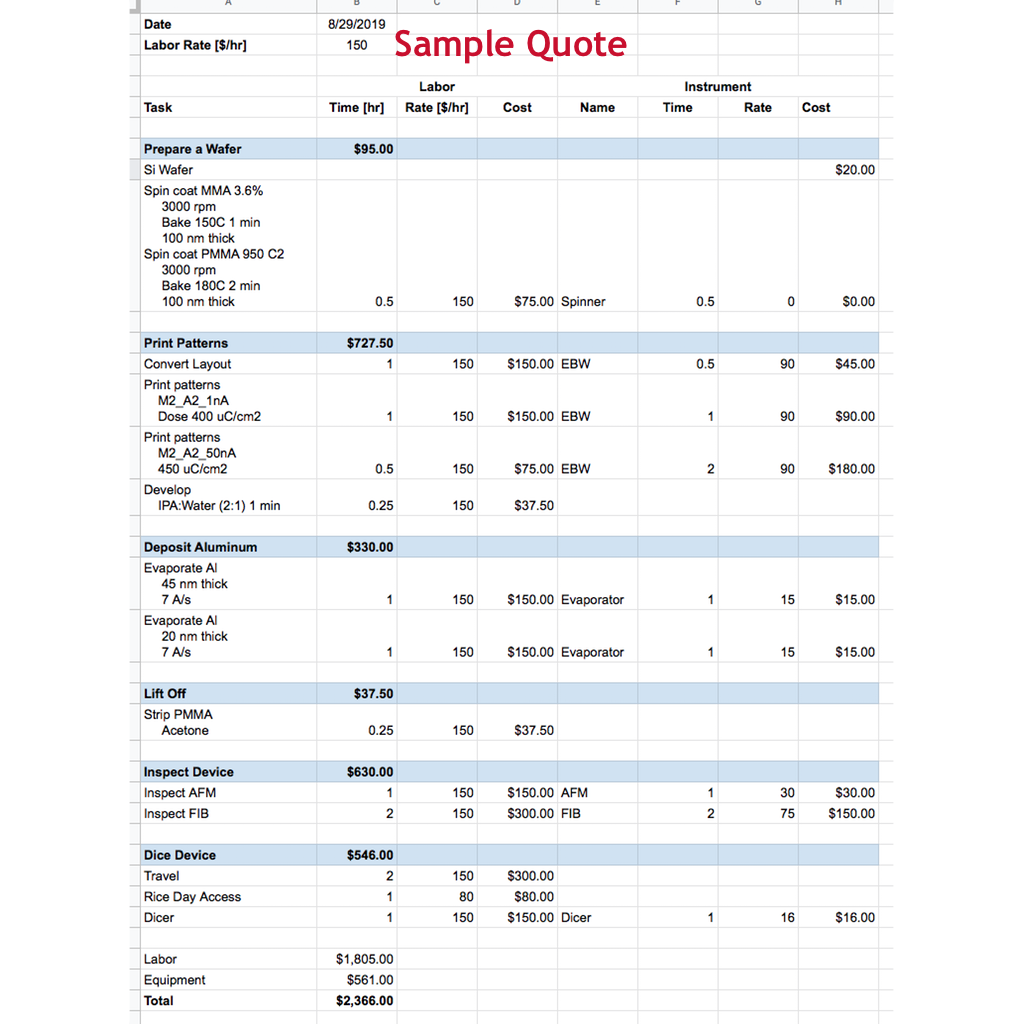
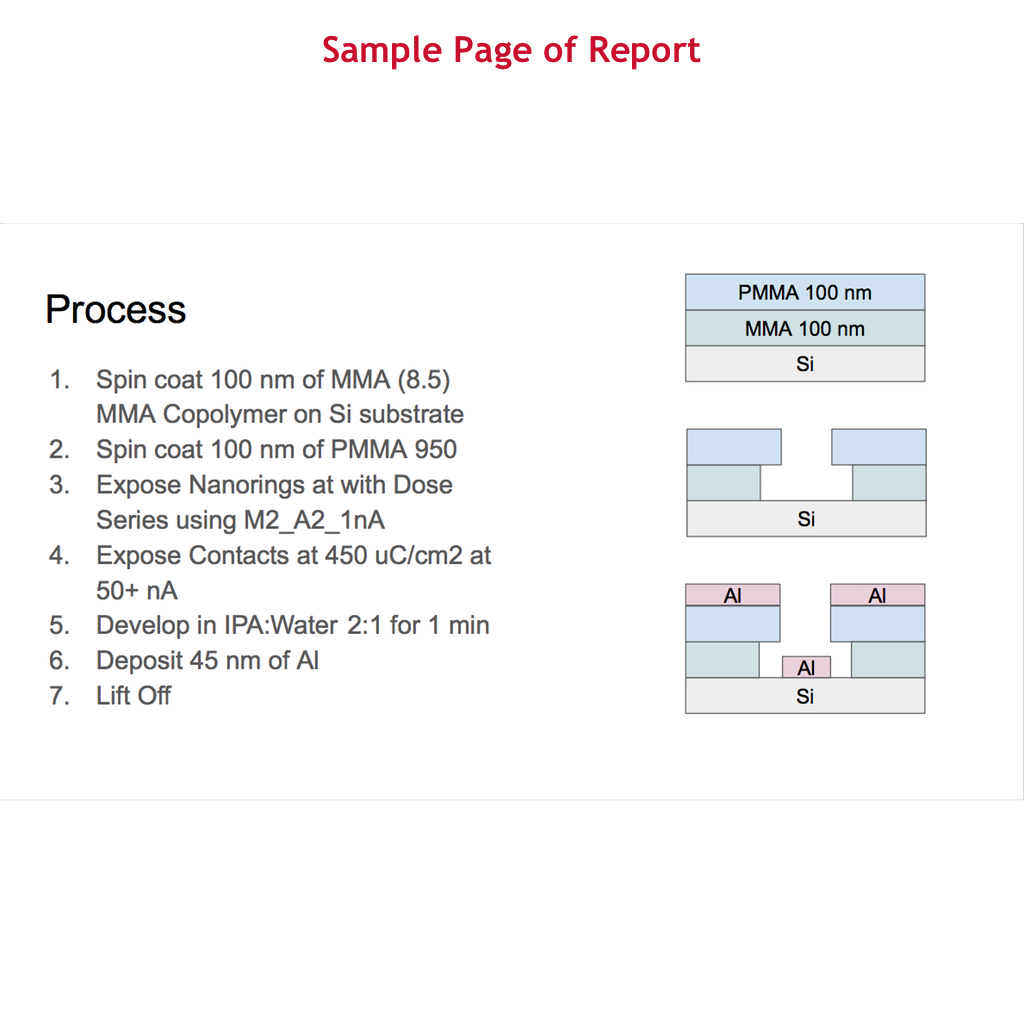
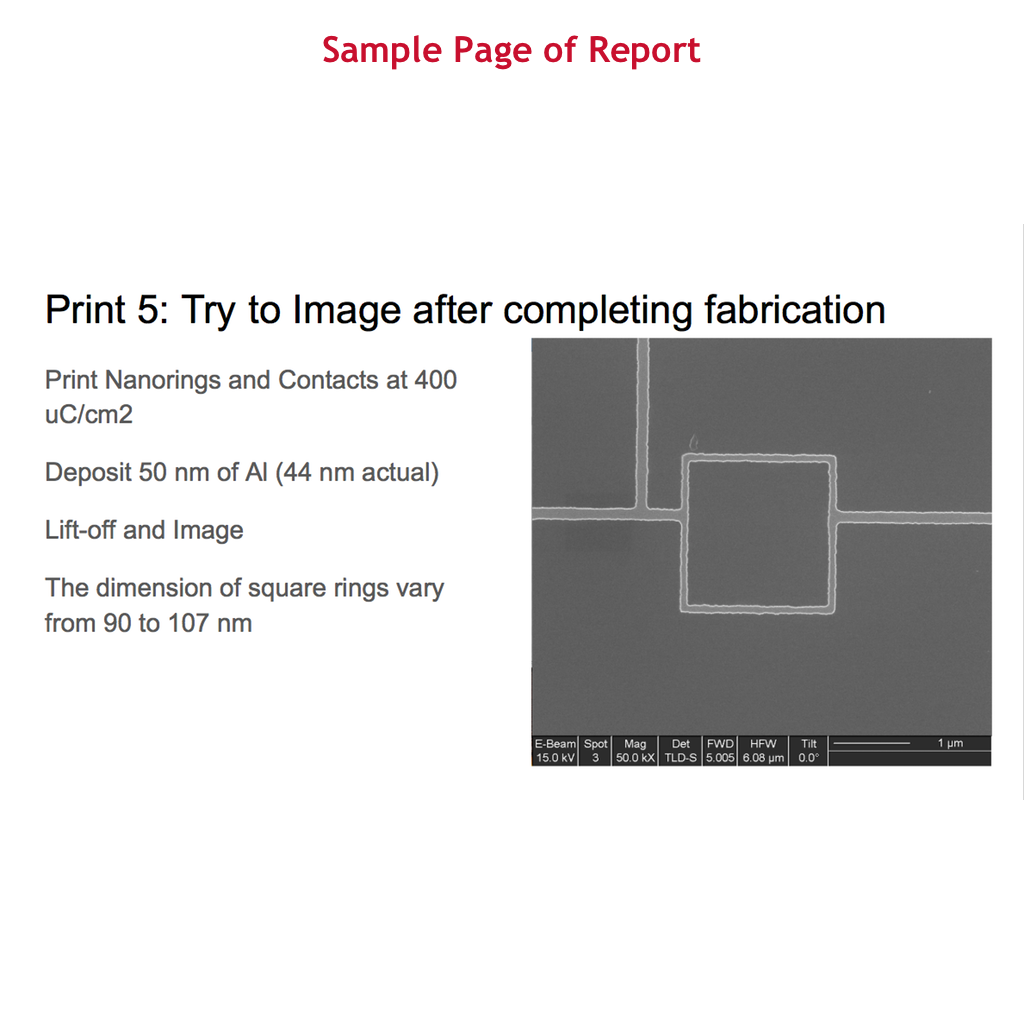
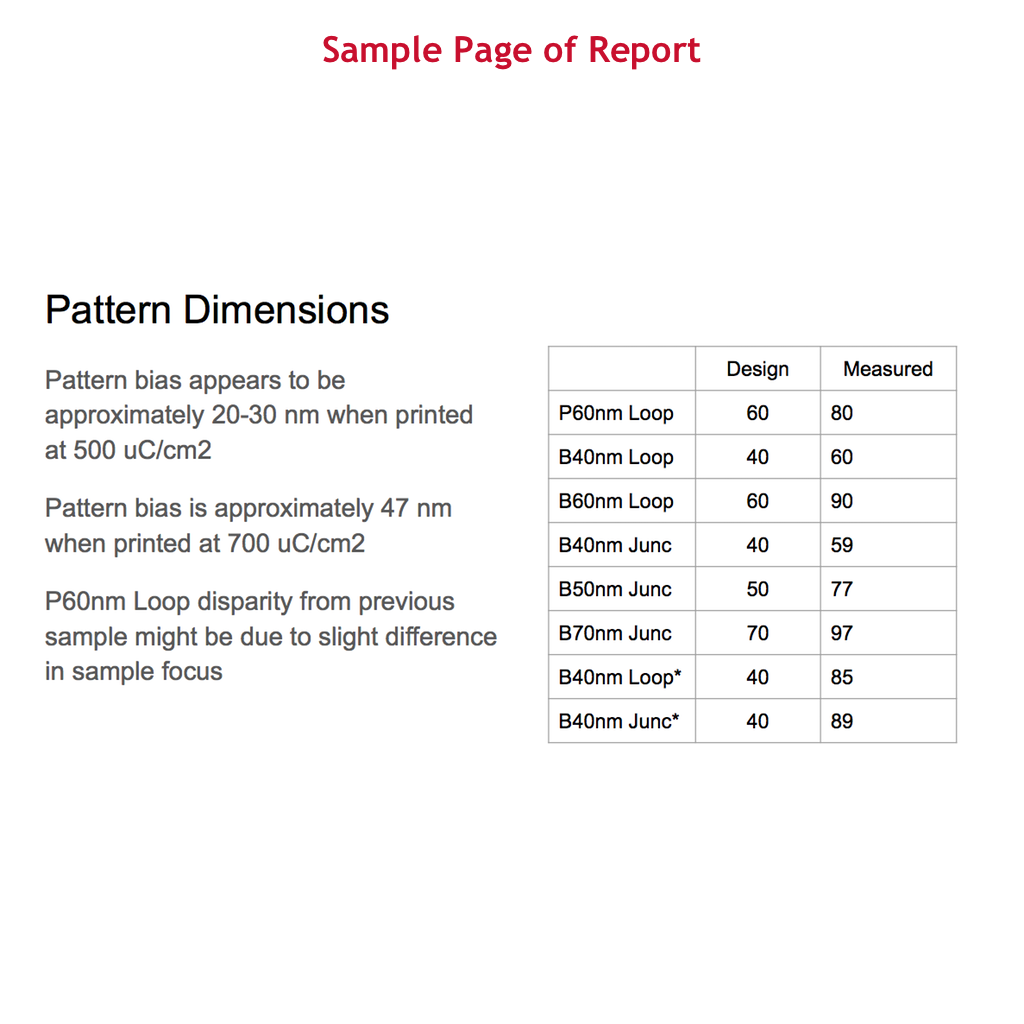
Video Explanation
Examples
SQUID-like Nanorings
A physicist from Florida State University inquired about our fabrication services in August 2019. After discussing the project, we saw an opportunity to fabricate the device at a lower cost by printing the device and contacts at the same time using the electron beam writer. We were able to produce devices with minimum feature dimensions of 56 [nm] connected to contacts that fill a 9 x 9 [mm] chip. The process was reliable enough to produce another two sets of 8 chips two and five months later. For this project, we visited Rice University to learn how to use a dicing saw to provide a sample dicing service. UHNF absorbed 100% of the research and development cost to produce new core capabilities and develop staff skills.
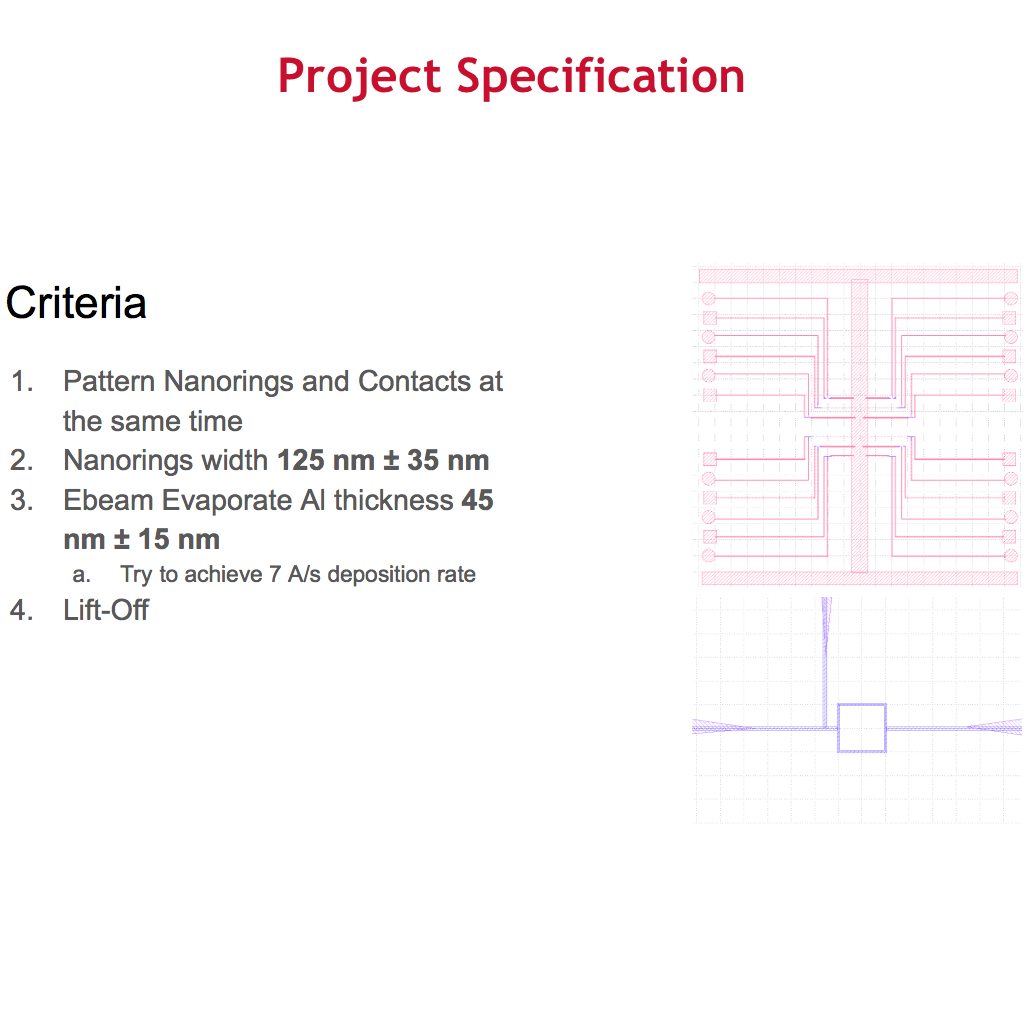
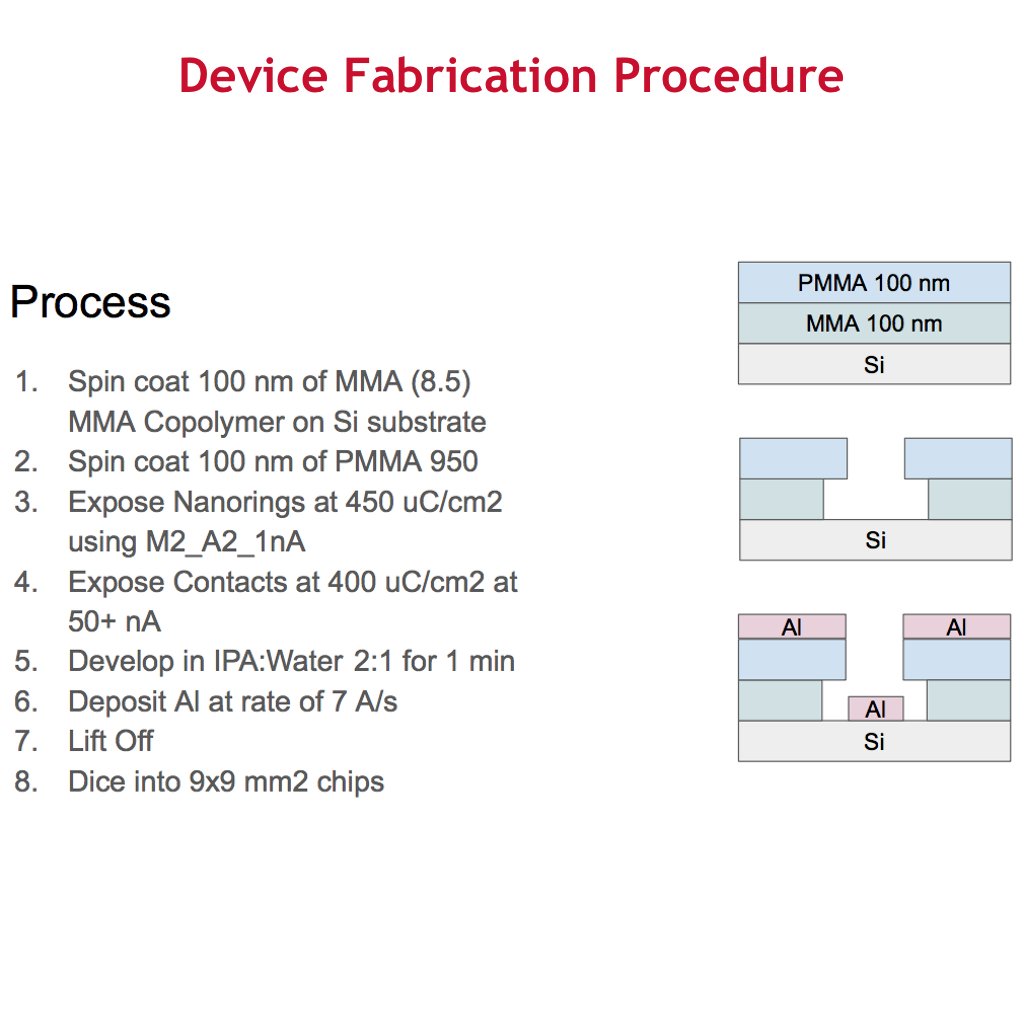
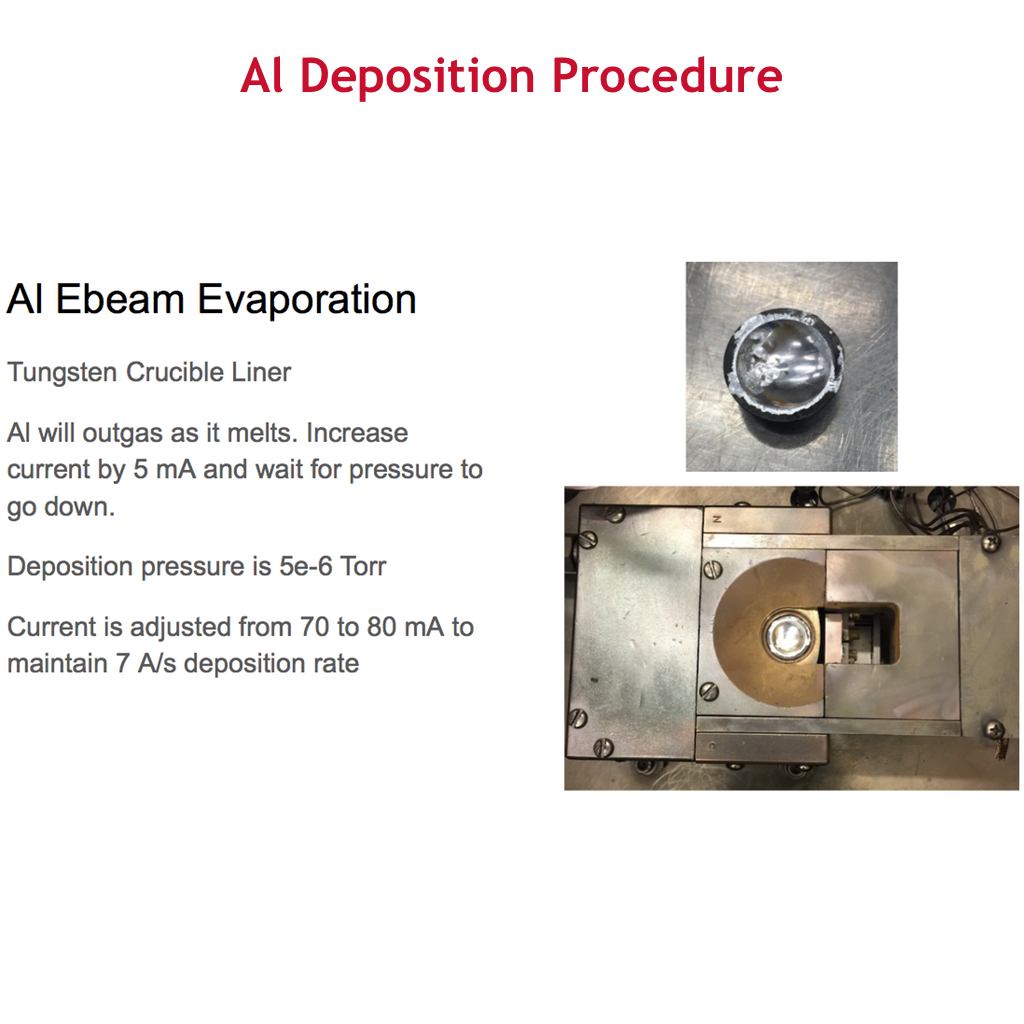
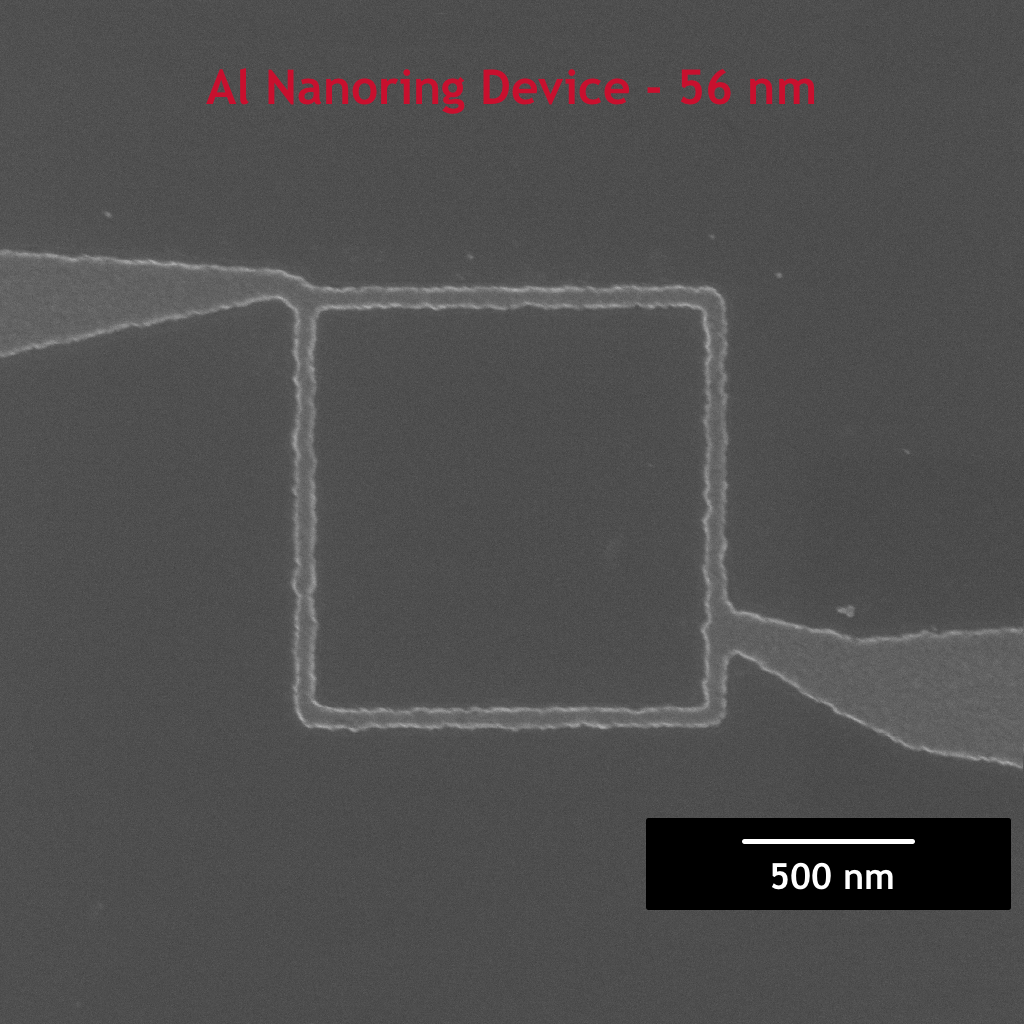
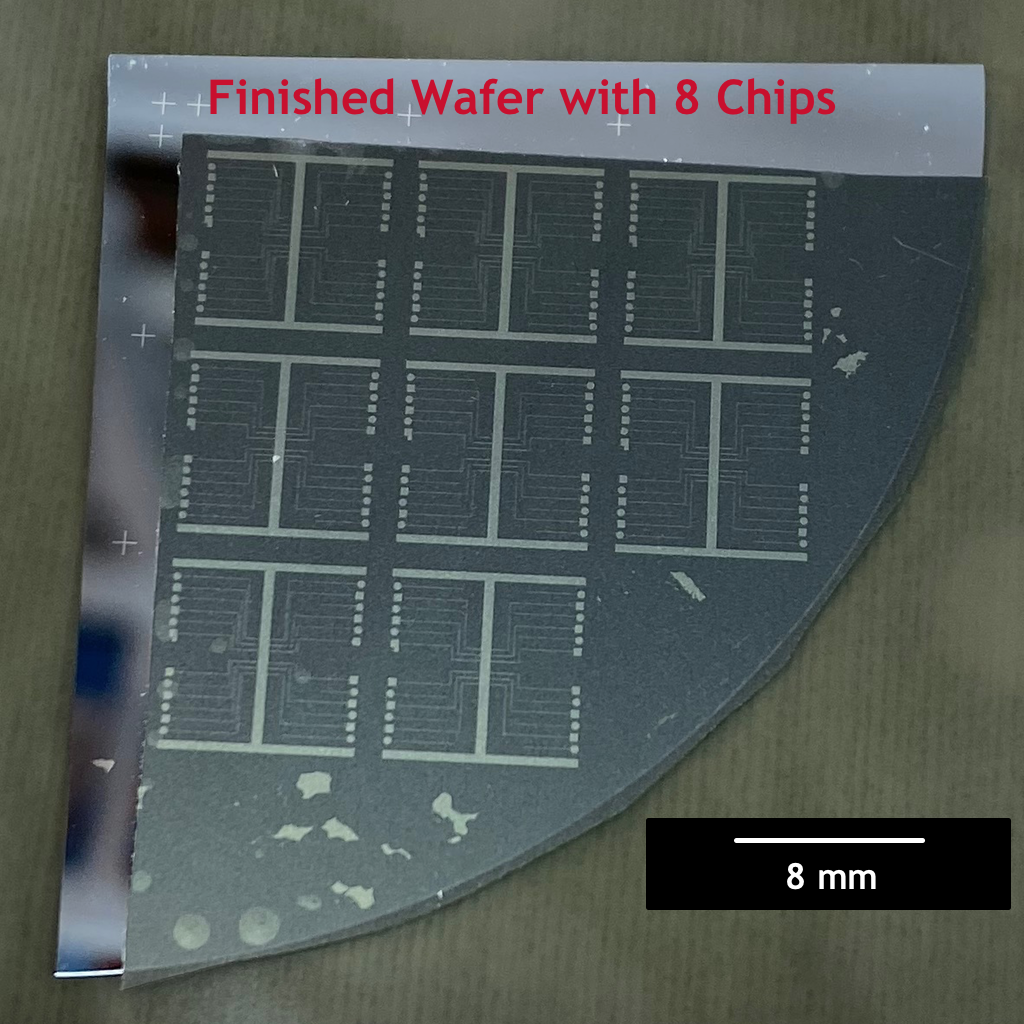
Surface Plasmon Polariton Metasurfaces
An Assistant Professor of Physics at the University of Texas Rio Grande Valley visited UHNF in the summer of 2017. After discussing the project, we recommended a non-traditional approach to fabricate his gadget that delegates the challenging tasks to staff and the easy tasks to his group because he needs a working sample a soon as possible as proof of concept for a grant proposal. A staff spent a week to fabricate a mold with the specified patterns using a core technology developed just 3 months earlier. We trained his group to use the mold to imprint the pattern and then transfer that pattern into their material by reactive ion etching. After several visits, they were able to realize a conceptual device that produces an optical response predicted by their finite-difference time-domain simulations.
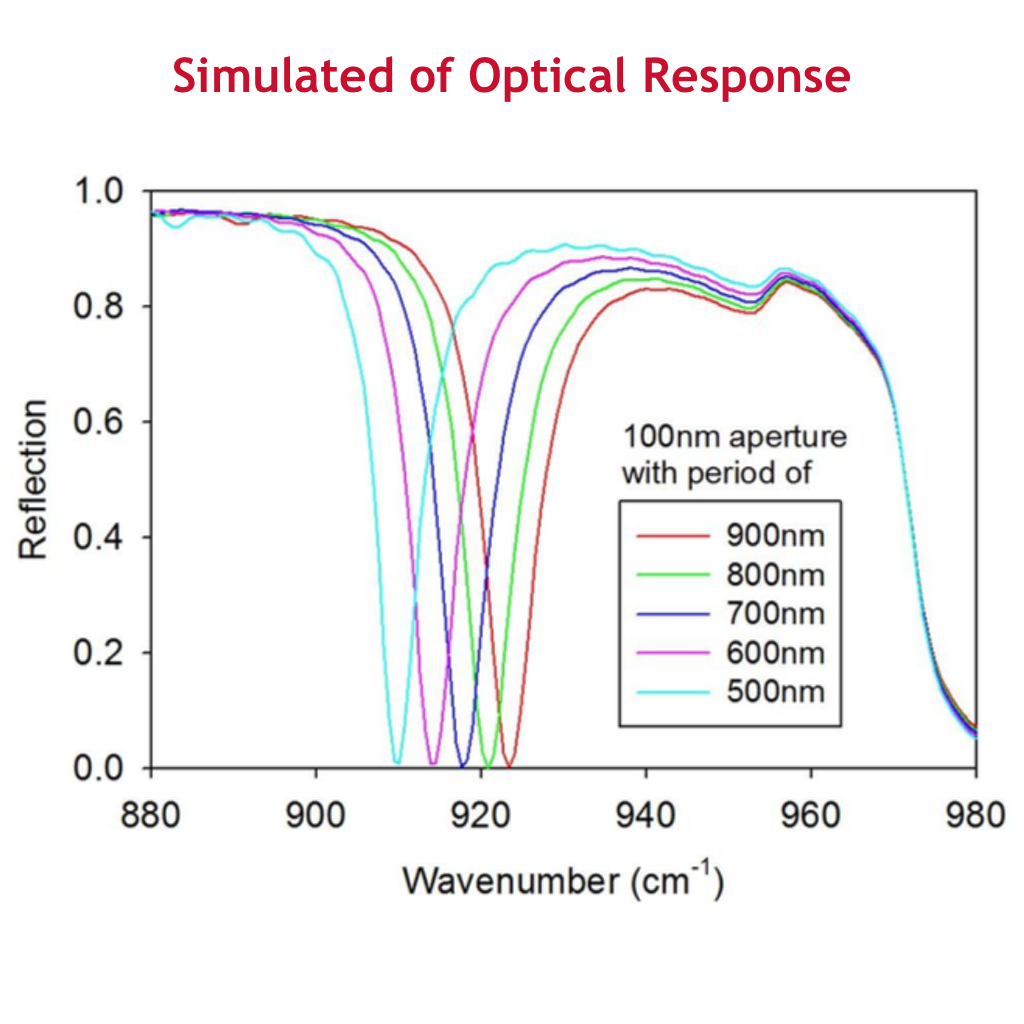
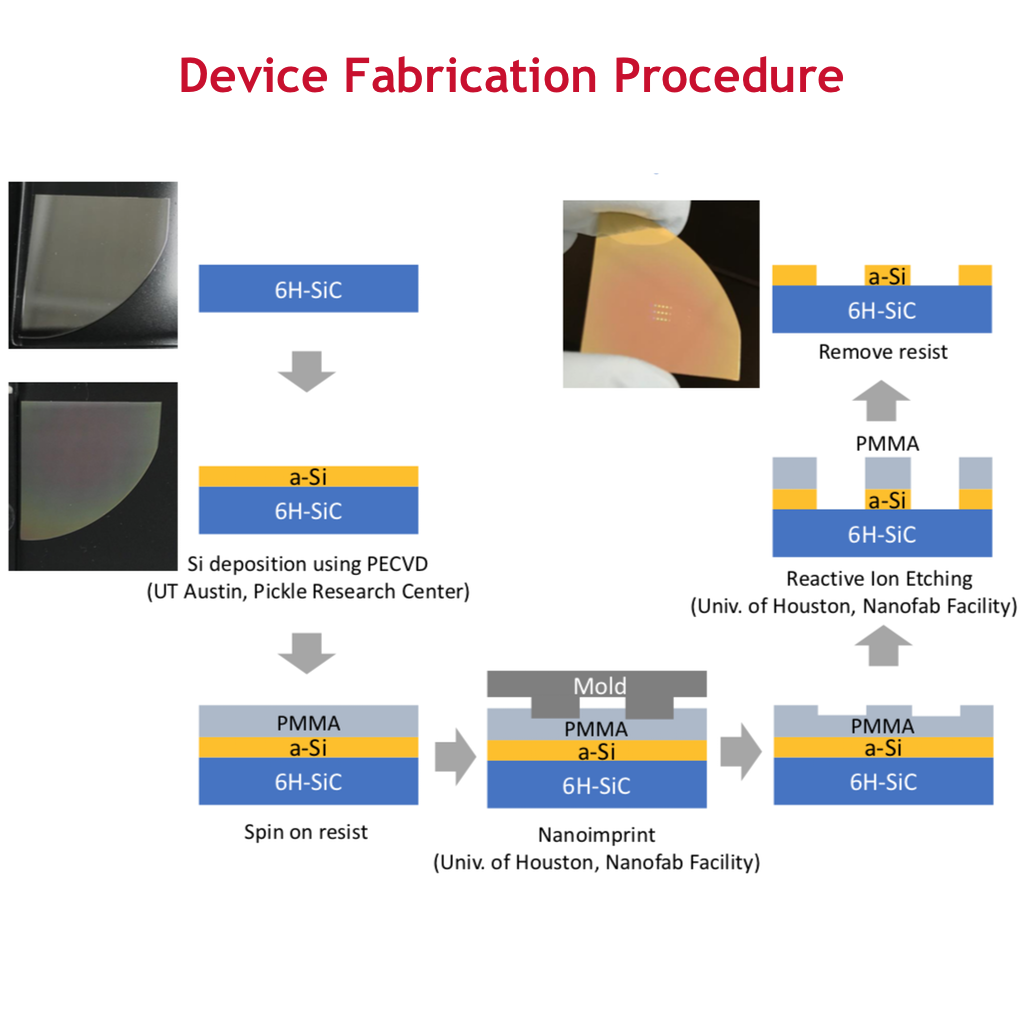
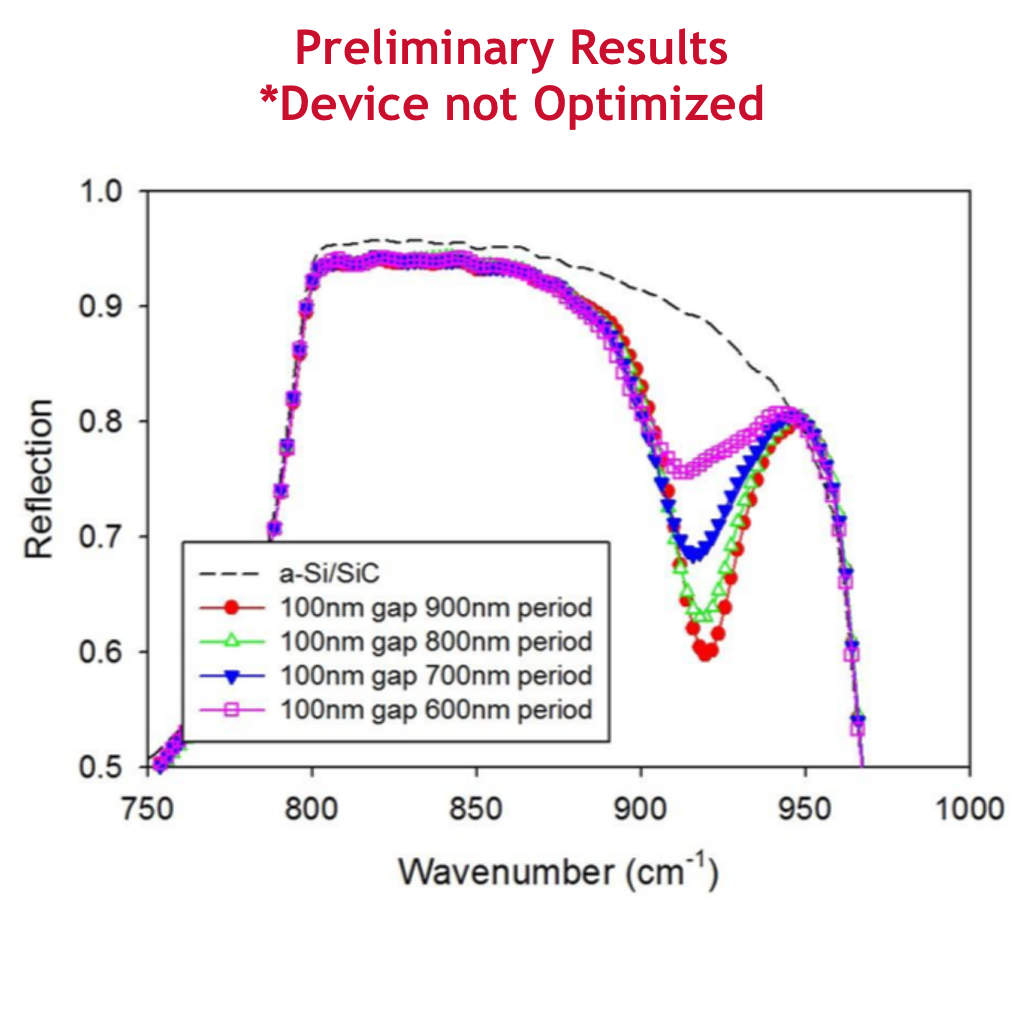